Unlocking Efficiency: Techniques for Selecting the Best Milling Tools for Your Needs
In the ever-evolving landscape of manufacturing, the selection of the right milling tools is paramount to unlocking efficiency and enhancing productivity. As industries push the boundaries to meet precision and quality standards, understanding the various types of milling tools available and their specific applications becomes crucial. This blog will delve into effective techniques for choosing the best milling tools tailored to your unique operational needs, ensuring that your machinery performs at its peak potential.
Understanding the intricate relationship between your projects and the appropriate milling tools can significantly impact not only the quality of the finished product but also the overall workflow efficiency. From assessing the material properties to considering the desired finish, the decision-making process can often seem overwhelming. However, with the right insights and strategies, selecting the ideal milling tools can transform your manufacturing process, driving both innovation and success in your endeavors. Join us as we explore practical tips and industry best practices to help you make informed choices in your milling operations.
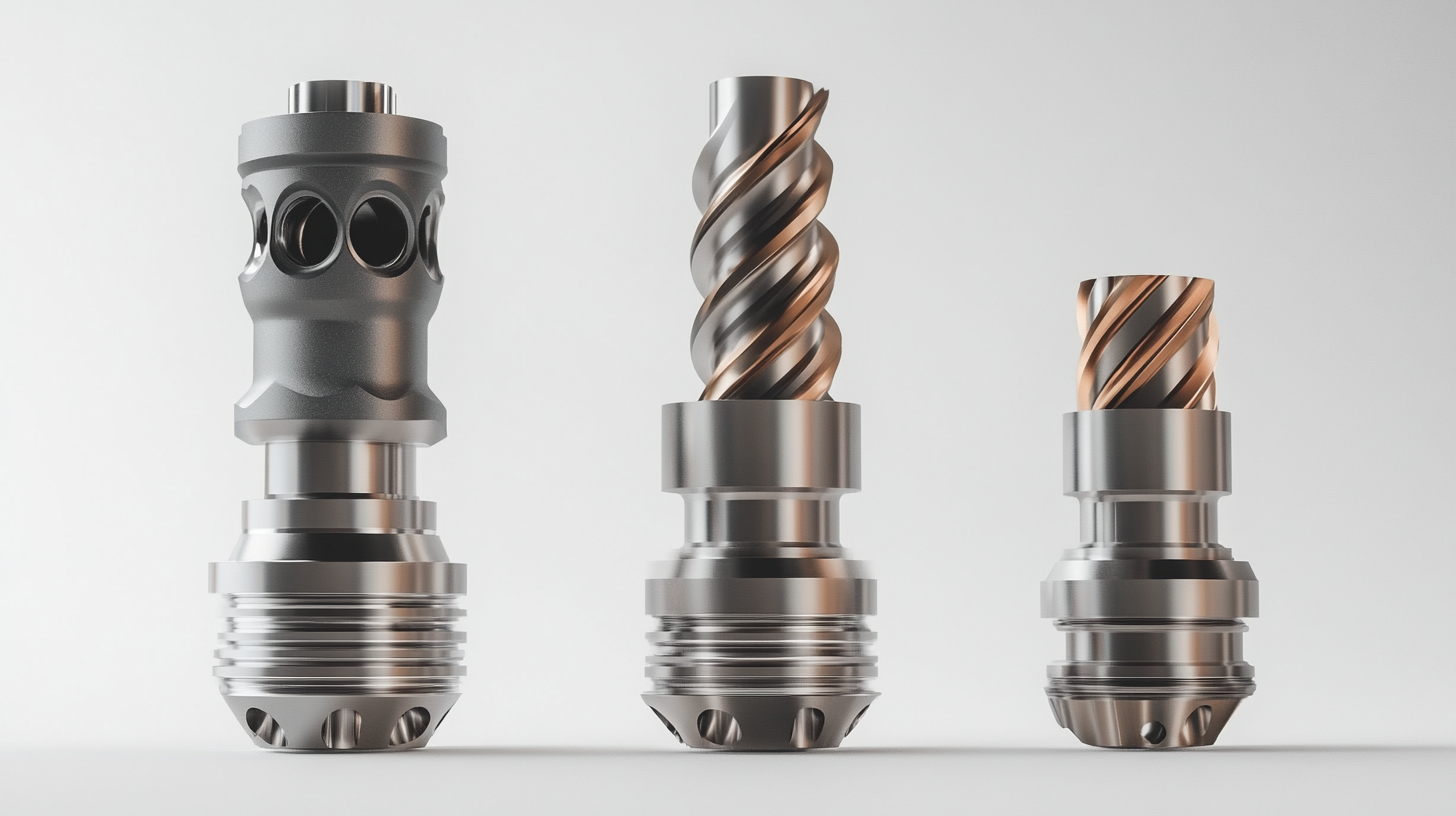
Understanding the Importance of Milling Tools in Manufacturing Efficiency
In the realm of manufacturing, milling tools play a pivotal role in shaping efficiency and precision. Their ability to remove material from a workpiece with high accuracy sets the foundation for the quality and performance of the final product. Understanding the importance of these tools is crucial for manufacturers seeking to optimize their processes and achieve their production goals. The selection of the right milling tool can significantly impact not only the efficiency of the machining process but also the longevity of the tool itself. Factors such as material compatibility, tool geometry, and cutting parameters must be considered for optimal results. A well-chosen milling tool reduces machining time and minimizes wear and tear, which leads to cost savings and improved output in manufacturing operations. Moreover, advancements in milling technology have led to the development of specialized tools designed for specific applications. By leveraging these innovations, manufacturers can enhance their machining capabilities, achieve tighter tolerances, and improve surface finishes. The right milling tool thus becomes an indispensable asset, forging a path toward greater manufacturing efficiency and competitiveness in today's fast-paced industrial landscape.
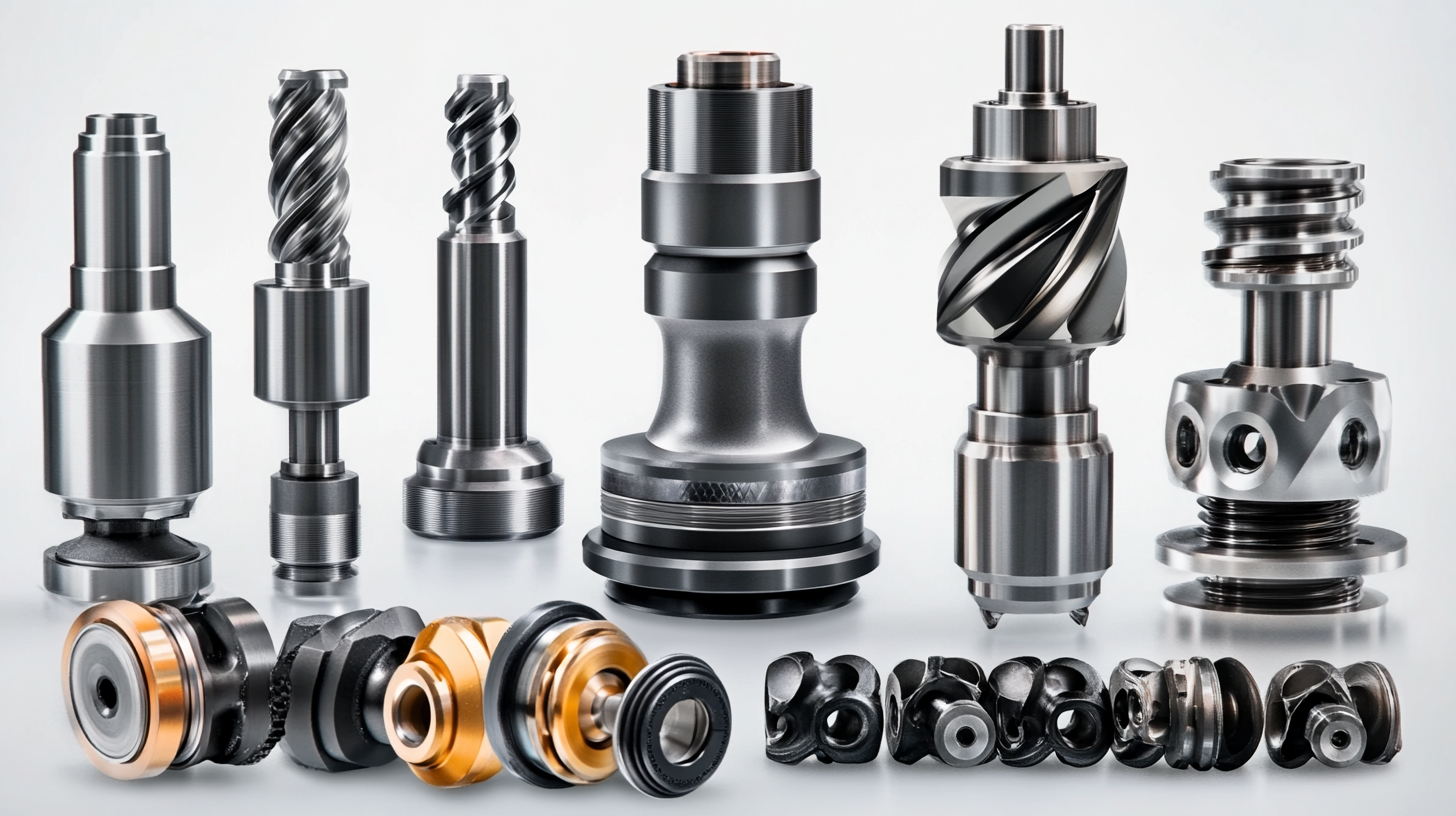
Key Factors to Consider When Choosing Milling Tools for Specific Applications
When it comes to milling, selecting the right tools can significantly influence productivity and the quality of the final product. One of the primary factors to consider is the material you will be working with. Different materials, such as aluminum, steel, or plastics, require specific cutting tools that can withstand the unique properties of each material. For instance, carbide tools are often preferred for harder materials due to their durability and resistance to wear, while high-speed steel may suffice for softer materials.
Another important factor is the type of milling operation you intend to perform. Face milling, end milling, and slot cutting each have distinct requirements in terms of tool shape and geometry. Understanding the specifics of your milling operation will help you choose tools designed for optimal performance. Additionally, consider the cutting parameters, such as speed and feed rates, which should align with the tool specifications to enhance efficiency and prevent tool failure.
Lastly, the desired finish and tolerances of your workpiece should guide your selection process. If a fine finish is essential, investing in high-precision tools with specific coatings may be necessary. Always balance the initial investment in quality tools against the expected longevity and performance, as this can lead to effective cost savings in the long run. By carefully evaluating these factors, you can unlock greater efficiency in your milling operations and achieve superior results.
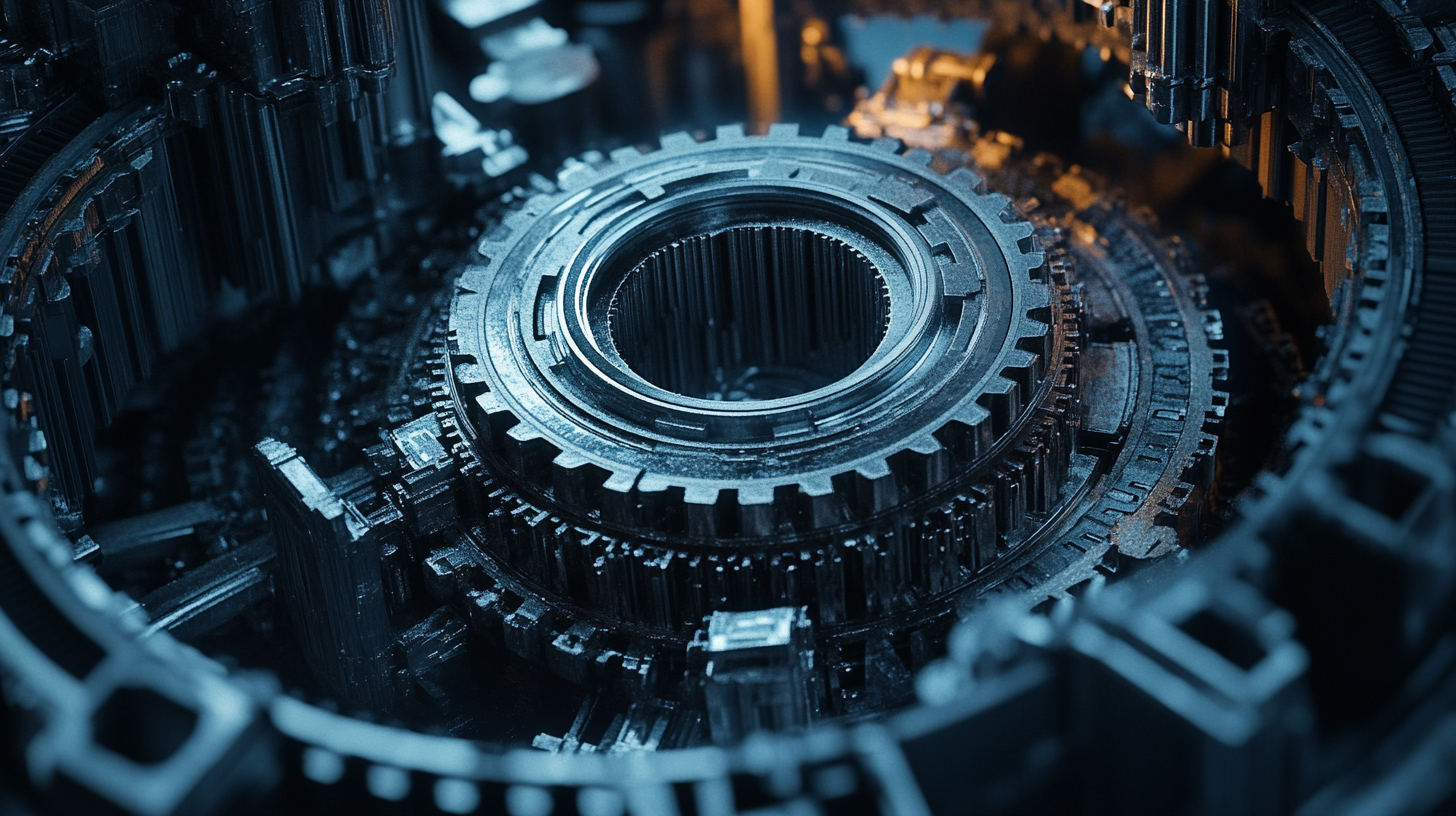
Comparing Different Types of Milling Tools: Pros and Cons
When it comes to milling tools, selecting the right one can significantly impact both efficiency and output quality. Different types of milling tools come with their unique advantages and drawbacks, making it crucial to understand these factors when making a decision. For instance, end mills are versatile and widely used, perfect for producing complex shapes and contours. They can handle a variety of materials, but their design may lead to faster wear compared to other tools, particularly in high-speed applications.
On the other hand, face mills excel at producing flat surfaces and can cover larger areas more quickly. Their ability to remove material at a faster rate is a significant advantage, yet they may not be as effective for intricate milling tasks, where precision is paramount. Additionally, the cost of face mills can be higher, especially if the inserts need frequent replacements.
Lastly, ball mills are particularly suited for tasks requiring a high degree of smoothness in the final product, making them ideal for finishing operations. However, this precision comes at the cost of speed, as ball mills tend to operate slower than their counterparts. Understanding the pros and cons of these milling tools will help you choose the best fit for your specific needs, ultimately leading to enhanced productivity and reduced operational costs.
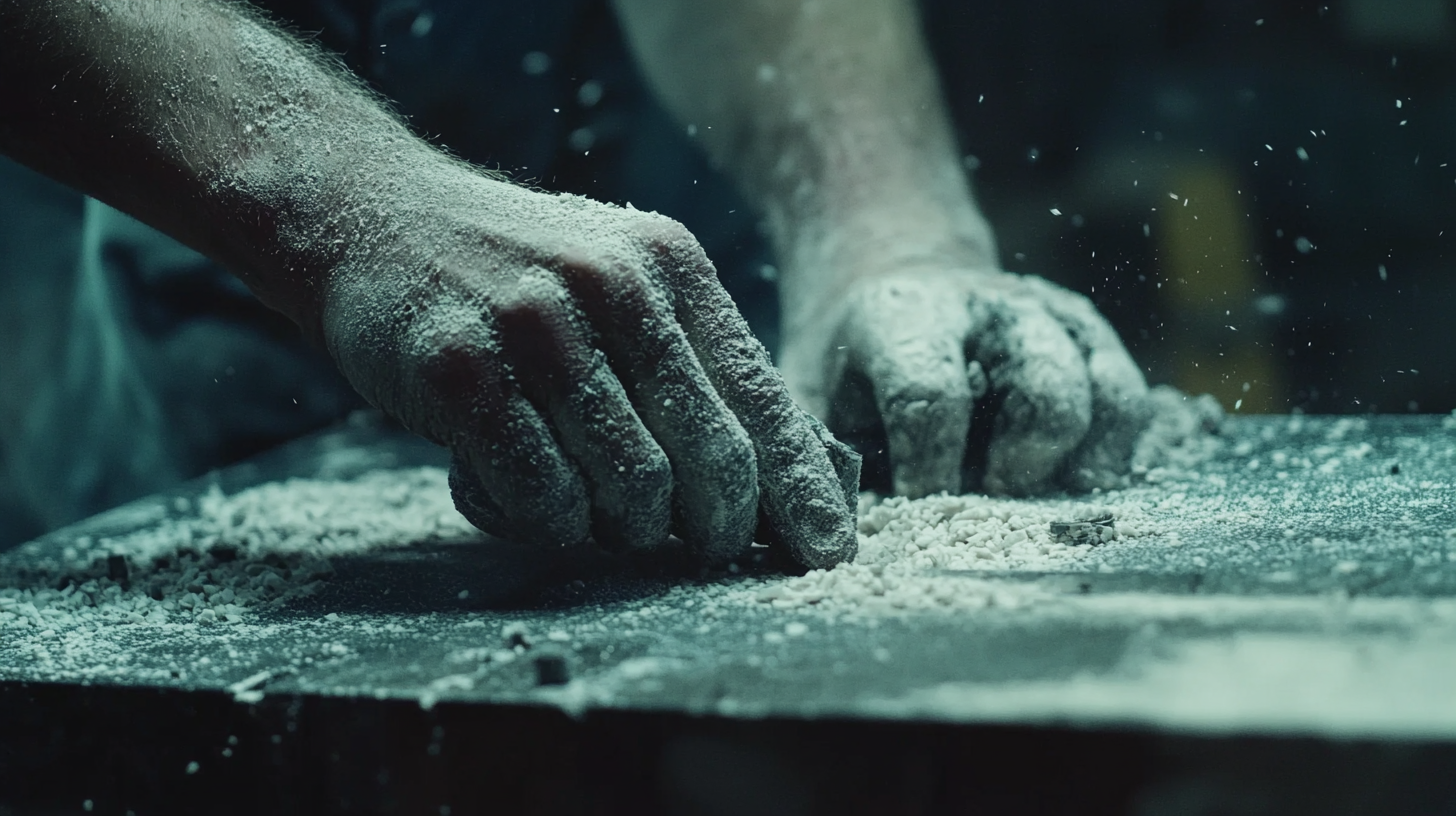
Innovative Technologies Enhancing Milling Tool Performance and Selection
In today’s fast-paced manufacturing landscape, the selection of milling tools is more crucial than ever. Innovative technologies are revolutionizing how we approach tool performance, delivering solutions that enhance precision and efficiency. Advanced materials such as carbides and ceramics have emerged, allowing for greater durability and longer tool life compared to traditional materials. These innovations not only reduce the frequency of tool changes but also minimize production downtime, leading to significant cost savings for manufacturers.
Moreover, the integration of smart technology into milling operations is transforming the decision-making process for tool selection. Real-time monitoring systems can analyze tool wear and performance data, enabling operators to select the most appropriate tools based on specific machining tasks. This proactive approach not only improves tool selection accuracy but also optimizes the entire milling process. By leveraging data analytics, manufacturers can achieve unprecedented levels of efficiency, ensuring that they remain competitive in an ever-evolving market.
Additionally, advancements in CAD/CAM software are enhancing the design and simulation of milling operations. These tools allow engineers to visualize machining scenarios and experiment with different milling tools in a virtual environment before actual production. As a result, manufacturers can make well-informed choices that maximize their machining capabilities while minimizing waste. This innovative blend of technology and expertise is setting a new standard for milling tool performance, driving the industry toward greater efficiency and productivity.
Maintenance Practices to Extend the Life of Your Milling Tools
When it comes to milling tools, maintenance practices play a crucial role in extending their lifespan and ensuring optimal performance. According to a report by the American Society of Mechanical Engineers (ASME), proper maintenance can increase the lifespan of milling tools by up to 30%. Regular inspection and timely servicing not only prevent premature wear but also enhance operational efficiency, ultimately reducing the overall cost of tooling.
One important practice in maintaining milling tools is implementing a strict cleaning schedule. Contaminants such as dust, chips, and coolant residues can accumulate, leading to corrosion and ineffective cutting. The Precision Tooling Association (PTA) suggests that periodic ultrasonic cleaning can be an effective method to remove stubborn residues. This practice, combined with proper storage methods—like using protective cases—can prevent damage and maintain the cutting edge integrity, ensuring that the tools function at peak performance.
Another key aspect of tool maintenance is sharpening. A report from the National Institute of Standards and Technology (NIST) indicates that dull tools can decrease machining efficiency by as much as 50%. Therefore, adopting a routine sharpening schedule based on the material being milled and the tool’s usage frequency is essential. Each type of milling tool has specific sharpening requirements, and adhering to these can significantly prolong the tool's effectiveness while maintaining high-quality output in milling operations.