Maximizing Your Investment in Machine Shop Tools Through Effective Maintenance Strategies
In today's fast-paced manufacturing landscape, the efficient operation of machine shop tools is crucial for staying competitive and maximizing productivity. These tools represent a significant investment for any machine shop, and their proper maintenance is key to ensuring that they perform at their best. Without effective maintenance strategies, the longevity and reliability of these tools can be compromised, leading to costly downtime and repairs. Therefore, understanding how to sustain and enhance the performance of machine shop tools is essential for achieving optimal returns on investment.
Effective maintenance strategies not only extend the lifespan of machine shop tools but also enhance their operational efficiency, ultimately contributing to improved product quality and profitability. By implementing a systematic approach to maintenance, shop owners and managers can minimize the risk of unexpected failures and breakdowns. In this blog, we will explore various maintenance practices that can help maximize your investment in machine shop tools, ensuring that your equipment continues to operate smoothly and efficiently for years to come.
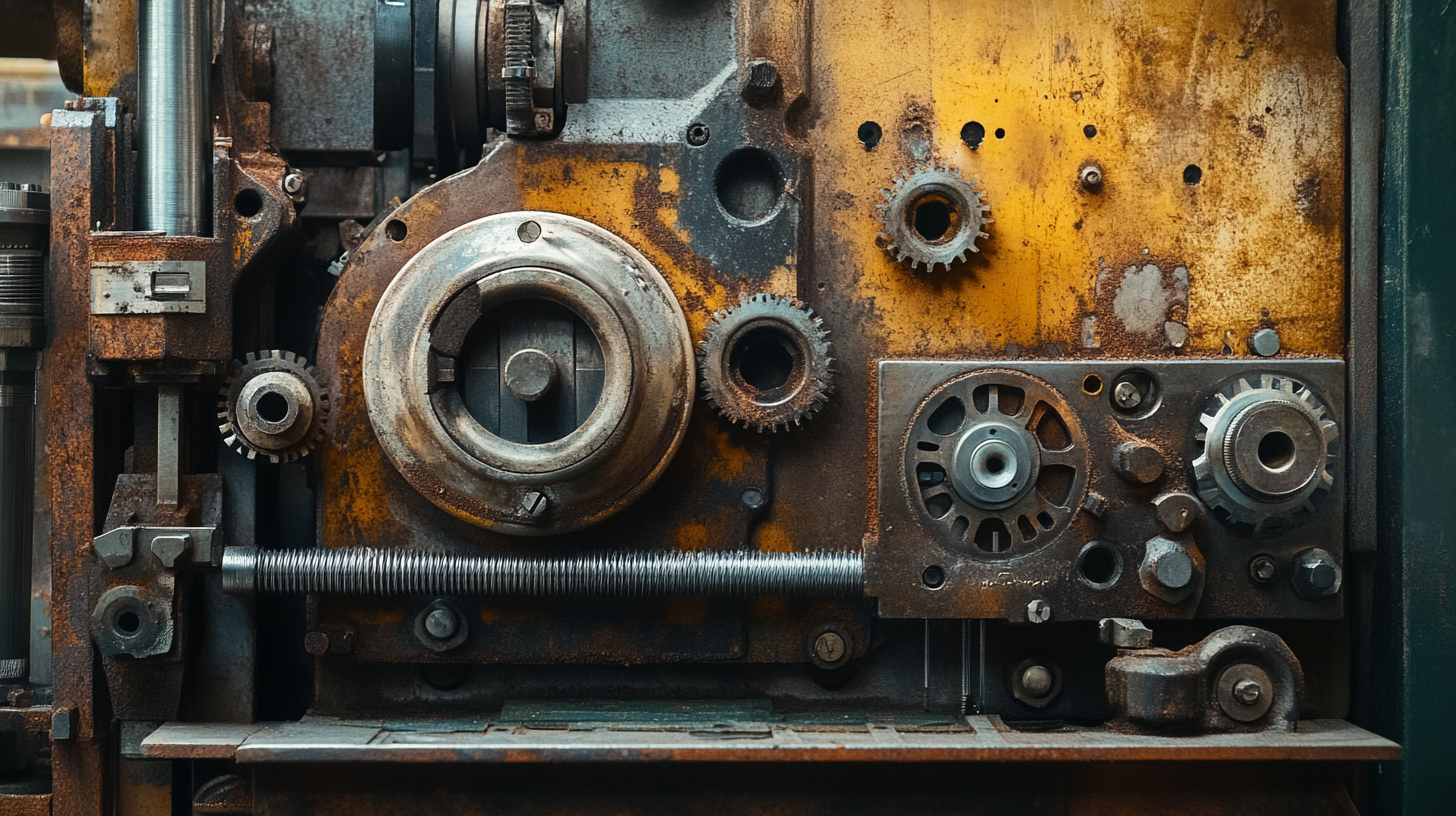
Understanding the Cost-Effectiveness of Regular Maintenance for Machine Tools
Regular maintenance of machine tools is not just a preventive measure; it’s a crucial investment strategy that significantly enhances the longevity and efficiency of your equipment. Machine tools are integral to any manufacturing operation, and their performance directly impacts productivity and profitability. By implementing a structured maintenance schedule, shop owners can identify potential issues before they escalate into costly breakdowns, saving both time and money in the long run. The cost-effectiveness of regular maintenance becomes evident when considering the twofold benefits it provides. Firstly, it reduces unforeseen repair costs, which can derail production schedules and lead to significant financial losses. Secondly, well-maintained tools operate more efficiently, maximizing their output and minimizing waste. This translates to a more streamlined operation where resources are used judiciously, ultimately enhancing the bottom line. Investing in training your staff to recognize maintenance needs and adhering to a routine check-up protocol can yield substantial returns. Simple tasks such as lubrication, calibration, and cleaning can prevent the more complex and expensive repairs that arise from neglect. Embracing a culture of proactive maintenance not only safeguards your investment in machine shop tools but also sets the groundwork for a more resilient and productive workshop.
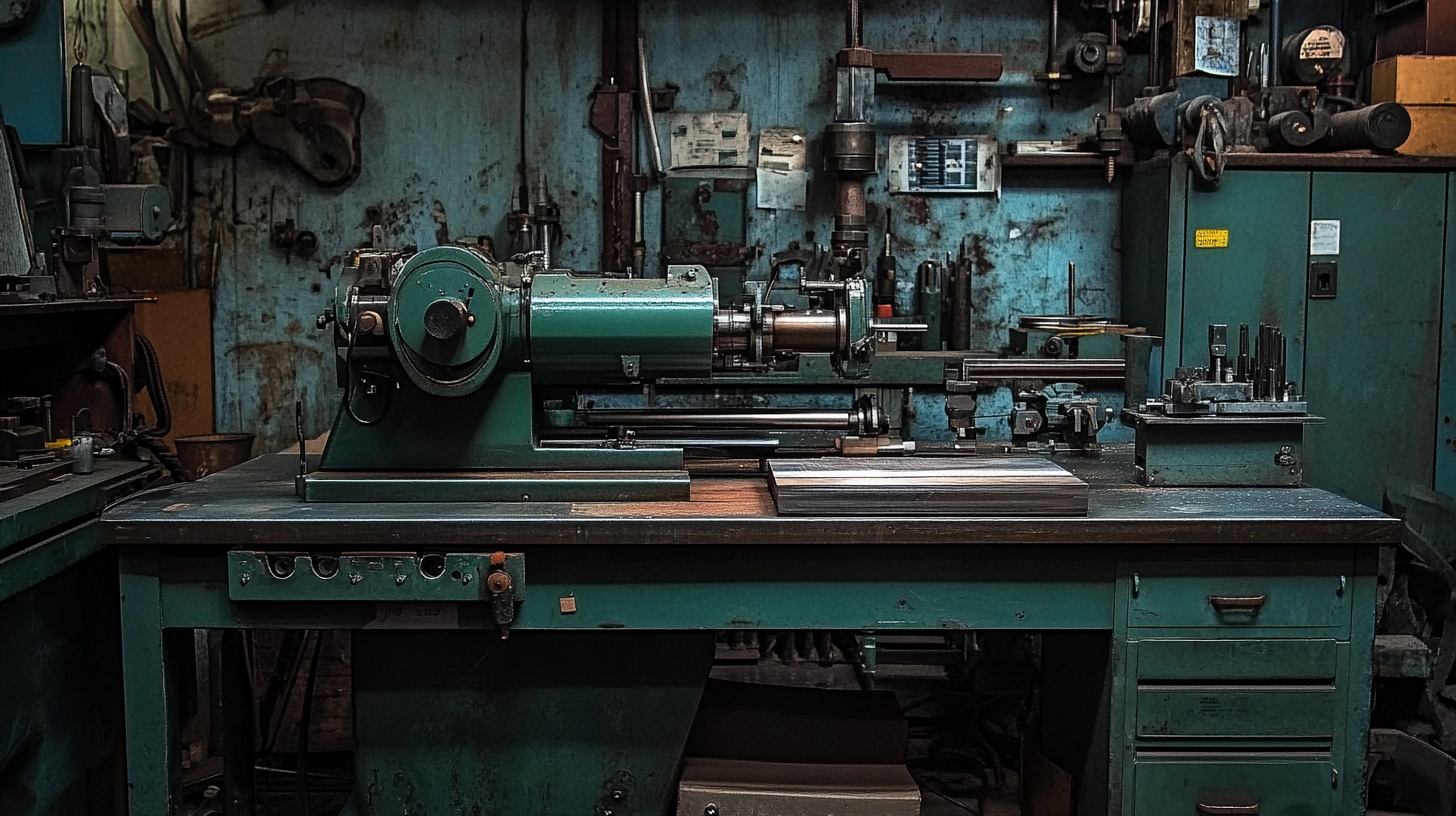
Identifying Key Maintenance Metrics to Maximize Tool Longevity and Performance
Effective maintenance strategies are crucial in ensuring the longevity and performance of machine shop tools. Identifying the key maintenance metrics can significantly impact the overall productivity and cost-efficiency of operations. A study by the American Productivity & Quality Center (APQC) revealed that organizations prioritizing maintenance can achieve a 5-15% increase in their production efficiency. Therefore, focusing on metrics such as Mean Time Between Failures (MTBF) and Overall Equipment Effectiveness (OEE) can lead to substantial improvements.
MTBF is a fundamental metric that helps in understanding the reliability of machine tools. By analyzing this data, shop managers can pinpoint frequent failure points and implement targeted maintenance actions, ultimately reducing unexpected downtimes. According to a report by Reliabilityweb.com, companies that actively monitor MTBF can reduce their maintenance costs by up to 25%, demonstrating the financial benefits of focusing on this metric.
Another critical metric is OEE, which measures how effectively a manufacturing operation is utilized compared to its full potential. A 2021 study published in the Journal of Quality in Maintenance Engineering highlighted that organizations with a high OEE score, above 85%, typically enjoy better profitability and tool performance. This underscores the importance of effective maintenance schedules and proactive strategies. Leveraging both MTBF and OEE as key performance indicators can create a foundation for maximizing the investment in machine shop tools while ensuring that they deliver optimal performance over their intended lifespan.
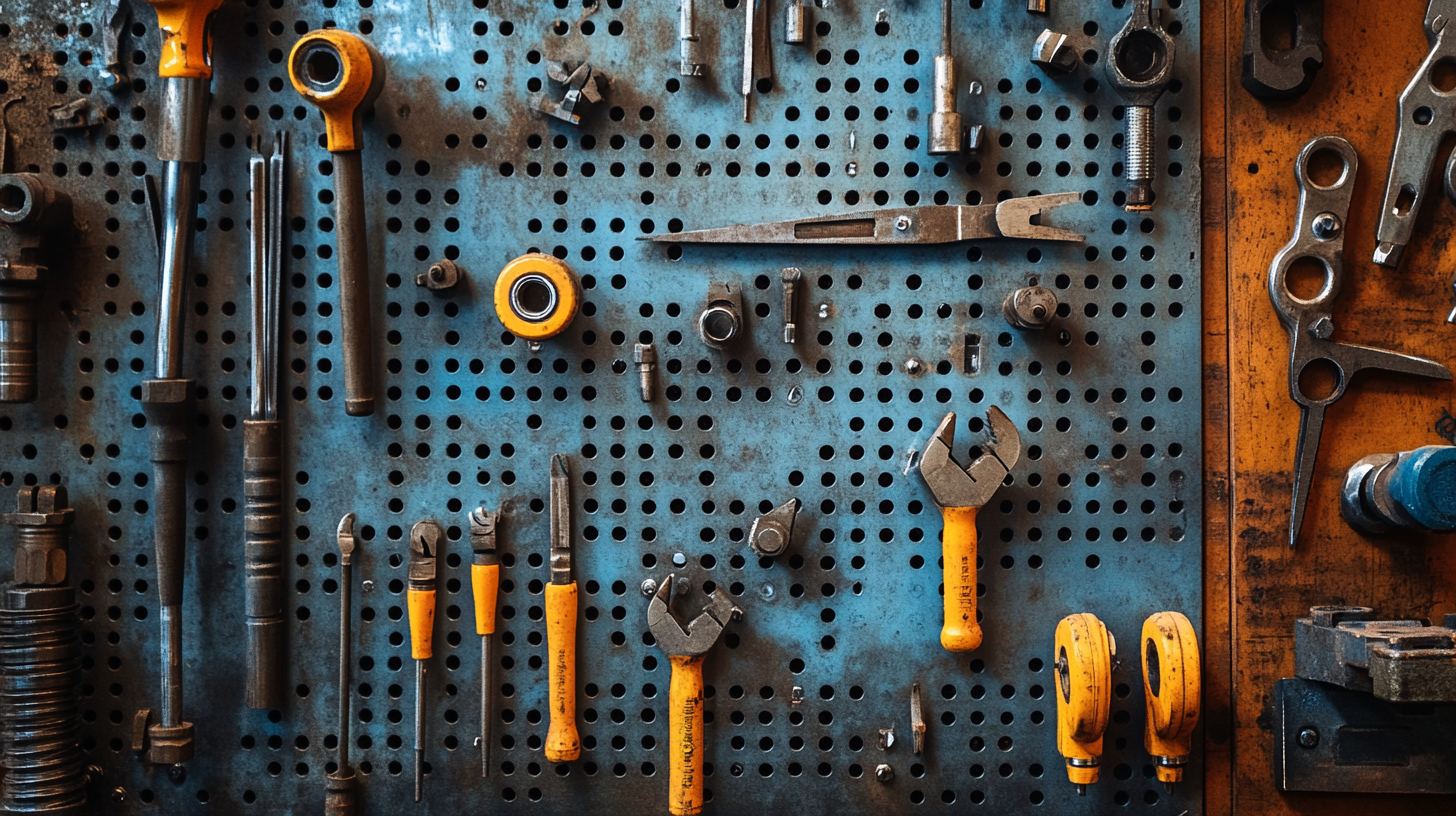
Implementing Preventive Maintenance Strategies to Reduce Downtime and Repair Costs
Implementing effective preventive maintenance strategies is crucial for reducing downtime and repair costs in a machine shop. A well-structured maintenance program not only extends the life of your tools but also ensures they function at optimal efficiency. By scheduling regular inspections and servicing, shop owners can identify potential issues before they escalate into costly repairs. This proactive approach minimizes unexpected breakdowns and keeps production running smoothly.
One key aspect of preventive maintenance is the establishment of a routine checklist tailored to each tool's specific needs. This checklist should include daily, weekly, and monthly tasks such as lubrication, cleaning, and calibration. By adhering to this schedule, machinists can enhance precision and performance, while also preventing wear and tear that could lead to significant downtime. Additionally, training staff on proper maintenance procedures fosters a culture of care and accountability within the team.
Another effective strategy is to leverage technology for monitoring tool condition. Implementing sensors and tracking software allows shops to gather real-time data on equipment performance. This information enables managers to make informed decisions about when to service tools, ensuring that maintenance is performed just in time to avoid disruptions. Investing in such technology not only reduces repair costs but also enhances productivity, making it a strategic choice for any forward-thinking machine shop.
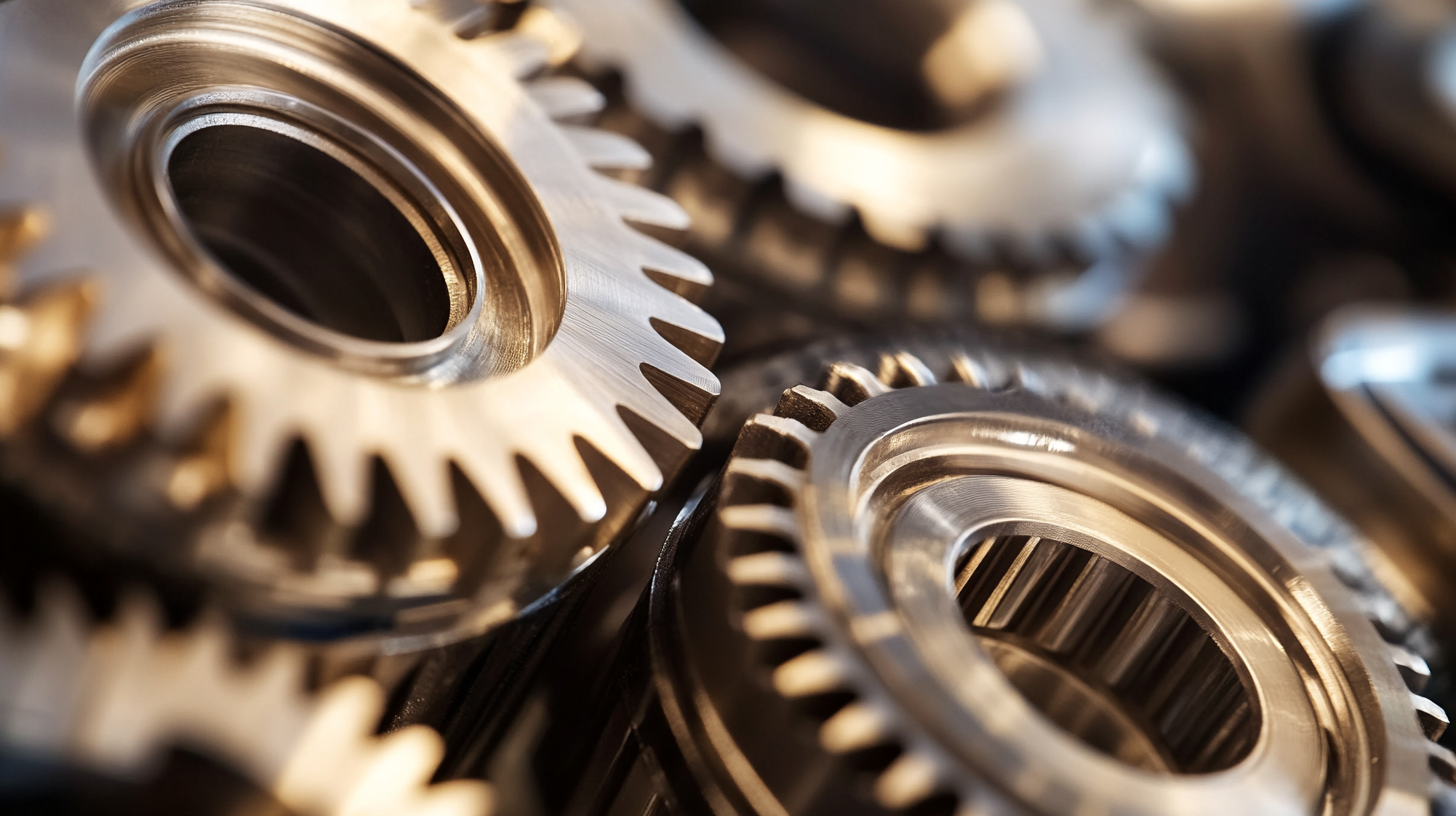
Leveraging Technology: How Predictive Maintenance Is Transforming Machine Shop Operations
In today's competitive manufacturing landscape, machine shops are increasingly turning to predictive maintenance to optimize tool performance and reduce downtime. According to a report by McKinsey, companies that adopt predictive maintenance can reduce maintenance costs by 20% to 25% and minimize equipment failures by up to 50%. This shift from traditional reactive maintenance to a more proactive approach empowers businesses to leverage advanced technology, enhancing operational efficiency.
The advent of the Internet of Things (IoT) and machine learning has made it possible for machine shops to monitor equipment health in real-time. Sensors collect data on vibrations, temperature, and other crucial parameters, feeding this information into predictive analytics platforms. A study published in the Journal of Manufacturing Systems indicates that implementing predictive maintenance can lead to a 10% improvement in operational effectiveness. By analyzing historical data and identifying trends, machine shops can schedule maintenance before potential failures occur, ensuring continuous production flow.
Moreover, the integration of cloud computing allows for scalable data processing capabilities, enabling small and medium-sized enterprises to harness the power of predictive maintenance without overwhelming their resources. According to a report from Gartner, organizations that adopt cloud-based predictive maintenance solutions can achieve a return on investment within 12 to 18 months. Consequently, machine shops that invest in these cutting-edge maintenance strategies are well-positioned to maximize their tool investments while staying ahead of market demands.
Case Studies: Successful Maintenance Practices from Top Machine Shops to Enhance Productivity
In the competitive world of manufacturing, machine shops are increasingly focused on boosting productivity while minimizing costs. One effective strategy to achieve these goals is through the implementation of robust maintenance practices. Case studies from top machine shops reveal how adopting systematic maintenance interventions can lead to significant enhancements in operational efficiency.
For instance, one leading machine shop adopted a predictive maintenance approach, utilizing advanced sensors and data analytics to monitor equipment health in real time. This proactive measure enabled them to forecast potential failures before they occurred, reducing unexpected downtime by over 30%. By shifting their focus from reactive repair strategies to preventive care, the shop not only maximized the life span of their tools but also streamlined their production schedules, leading to a more reliable output.
Similarly, another top-performing machine shop implemented a comprehensive training program for all floor employees, emphasizing the importance of regular machine checks as part of their daily routine. This culture of shared responsibility fostered a dedicated workforce that was more engaged and aware of the machines they operated. As a result, the shop saw a remarkable decrease in minor errors and maintenance requests, allowing skilled technicians to focus on more critical tasks, ultimately enhancing productivity across the board.