5 Essential Tips for Global Buyers: Maximizing ROI with Indexable Tooling in Manufacturing
In an increasingly competitive global manufacturing landscape, companies are under constant pressure to optimize their production processes and achieve higher returns on investment (ROI). A recent report from the International Federation of Robotics highlights that the adoption of advanced tooling solutions, such as Indexable Tooling, can significantly enhance operational efficiency and cost-effectiveness. Indexable Tooling not only reduces material waste but also accelerates machining times, positioning manufacturers to better respond to market demands. According to a study by IndustryWeek, manufacturers employing indexable inserts report upwards of 30% increase in productivity due to reduced downtime and improved tool life. As global buyers seek to maximize ROI, understanding the strategic advantages of Indexable Tooling becomes essential, paving the way for innovative practices that ensure long-term success in the dynamic world of manufacturing.
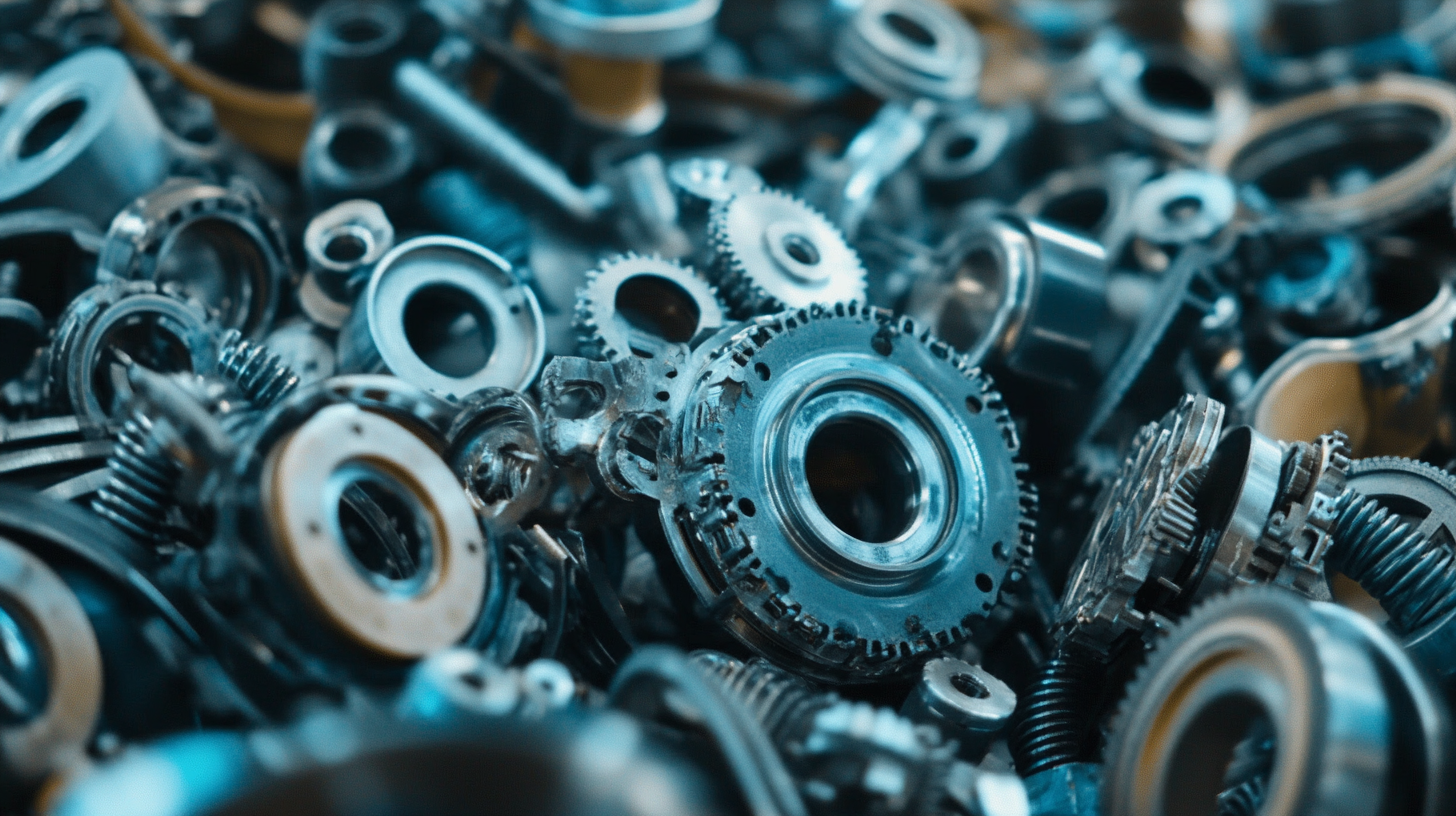
Understanding Indexable Tooling and Its Importance in Manufacturing
Indexable tooling plays a crucial role in modern manufacturing, particularly when it comes to maximizing efficiency and cost-effectiveness. Understanding the nuances of tooling can help global buyers make informed decisions that positively impact their return on investment (ROI). It's essential for manufacturers to focus on cost per part rather than just the initial cost per tool; this shift in perspective ensures a more accurate understanding of overall production costs and profitability.
The importance of recycling carbide tooling cannot be overstated. With an average recycle rate of 35% for carbide and even higher rates for metal cutting tools, manufacturers can significantly reduce waste and reclaim valuable materials. Choosing the right tools, such as advanced round tools, is also critical as they are increasingly favored in machining operations due to their ability to meet diverse market needs, providing enhanced performance and versatility.
As US cutting tool orders show an upward trend, it highlights the growing recognition of the value add that high-quality, indexable tooling brings to the manufacturing process. End users must weigh the options of repairing or replacing tools as they wear over time, understanding that proactive management can extend tool life and maintain operational efficiency. By investing wisely in tooling and maintenance, manufacturers can secure a stronger competitive edge in today's fast-paced market.
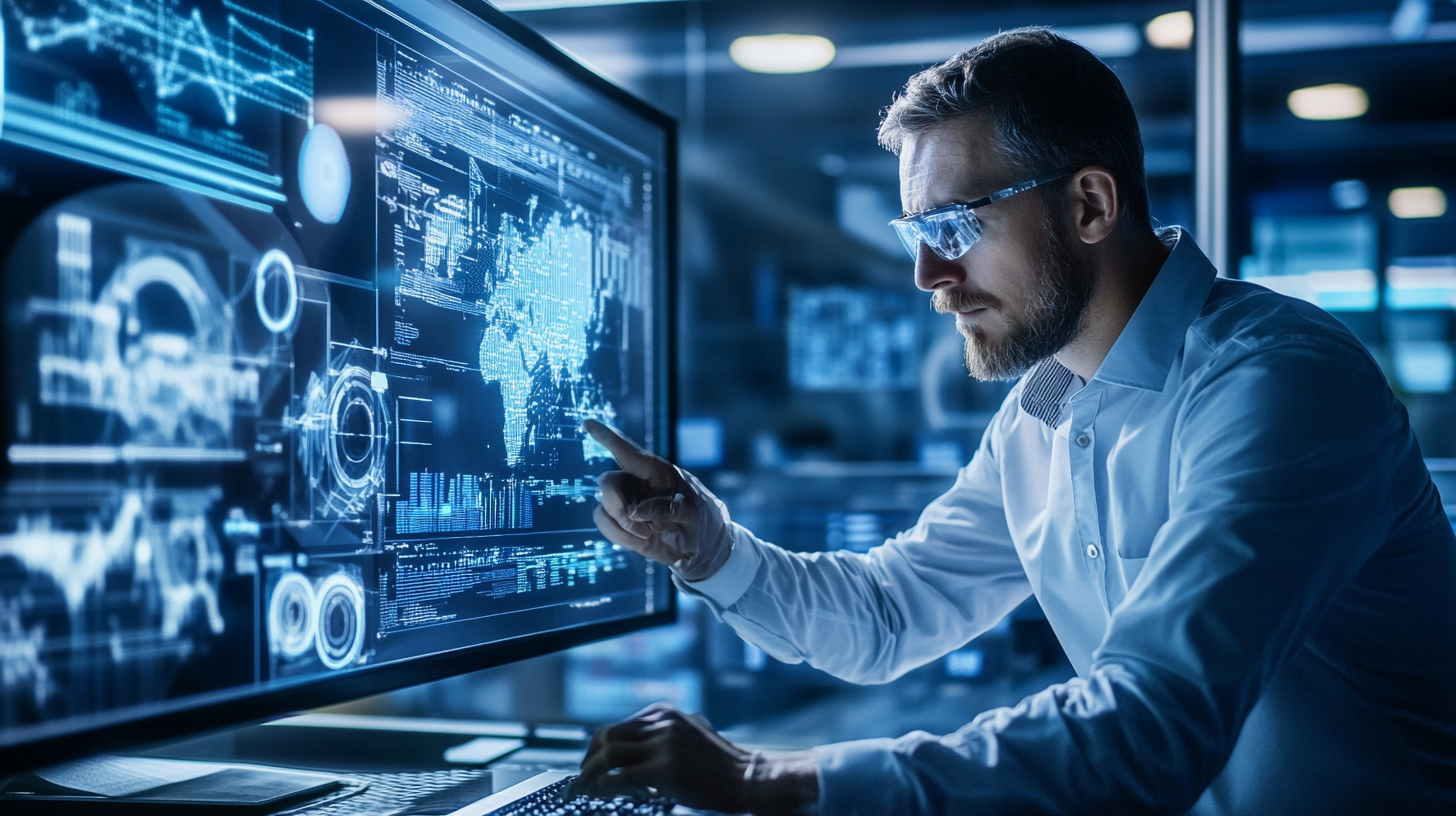
Evaluating Cost-Effectiveness: How Indexable Tooling Impacts ROI
When evaluating the cost-effectiveness of manufacturing processes, indexable tooling stands out as a critical factor influencing return on investment (ROI). Unlike traditional tooling methods, indexable tools offer the flexibility to change cutting inserts without replacing the entire tool, significantly reducing tool costs and downtime. This adaptability not only streamlines production but also enhances the ability to meet varying demands in different markets, allowing for a more agile manufacturing process.
Furthermore, the longevity and performance of indexable tooling play a crucial role in maintaining cost-effectiveness. High-quality inserts can withstand extensive use, leading to fewer tool changes and reduced maintenance costs. In industries where time is money, the ability to maximize uptime through durable tooling directly translates to increased productivity and profitability. As a result, manufacturers who invest in indexable tooling are better positioned to evaluate their cost structures, ensuring that each dollar spent contributes effectively to their bottom line.
Ultimately, understanding how indexable tooling impacts ROI is essential for global buyers aiming to optimize their manufacturing investments. By focusing on additional savings generated through increased efficiency, longevity, and performance, organizations can make informed decisions that foster sustainable growth while enhancing overall competitiveness in the global market.
Cost-Effectiveness of Indexable Tooling in Manufacturing
This pie chart illustrates the various factors contributing to the return on investment (ROI) when using indexable tooling in manufacturing. Understanding these elements can help global buyers make informed decisions to maximize their investments.
Best Practices for Selecting Quality Indexable Tooling Suppliers
Selecting quality indexable tooling suppliers is crucial for global buyers looking to maximize return on investment (ROI) in manufacturing. To make informed choices, it's essential to prioritize suppliers who adhere to industry best practices and regulatory standards, ensuring that their production processes are both efficient and ethically sound. Companies like Walmart set high benchmarks for supplier accountability, particularly concerning labor practices and sustainability measures, which should serve as a model for other buyers in the industry.
Additionally, leveraging advances in technology can enhance the supplier selection process. Tools that incorporate predictive analytics and AI capabilities allow buyers to make data-driven decisions about tooling purchases. By analyzing supplier performance and market trends, businesses can better assess potential risks and benefits associated with different suppliers. This strategic approach not only helps in selecting high-quality tooling but also positions manufacturers to respond swiftly to market changes and customer demands, ultimately driving greater profitability and sustainability in their operations.
Implementing Indexable Tooling for Efficient Production Cycles
The implementation of indexable tooling in manufacturing is revolutionizing production efficiency across various industries. According to a report by Technavio, the global indexable tooling market is expected to grow by over 5% annually from 2021 to 2026, indicating a significant shift towards more adaptable and economically viable machining solutions. Indexable tools offer the flexibility of replacing only the cutting inserts rather than entire tool assemblies, which not only reduces costs but also minimizes downtime during production cycles.
In addition, a case study published by the Society of Manufacturing Engineers demonstrates that companies utilizing indexable tooling have improved their production cycle times by up to 30%. This increase in efficiency is largely attributed to the ease of tool changes and the extended life of cutting edges, enabling manufacturers to achieve higher levels of precision while maintaining a competitive edge. As global buyers seek to maximize return on investment, adopting indexable tooling emerges as a strategic approach to streamline operations and drive profitability in an increasingly challenging market environment.
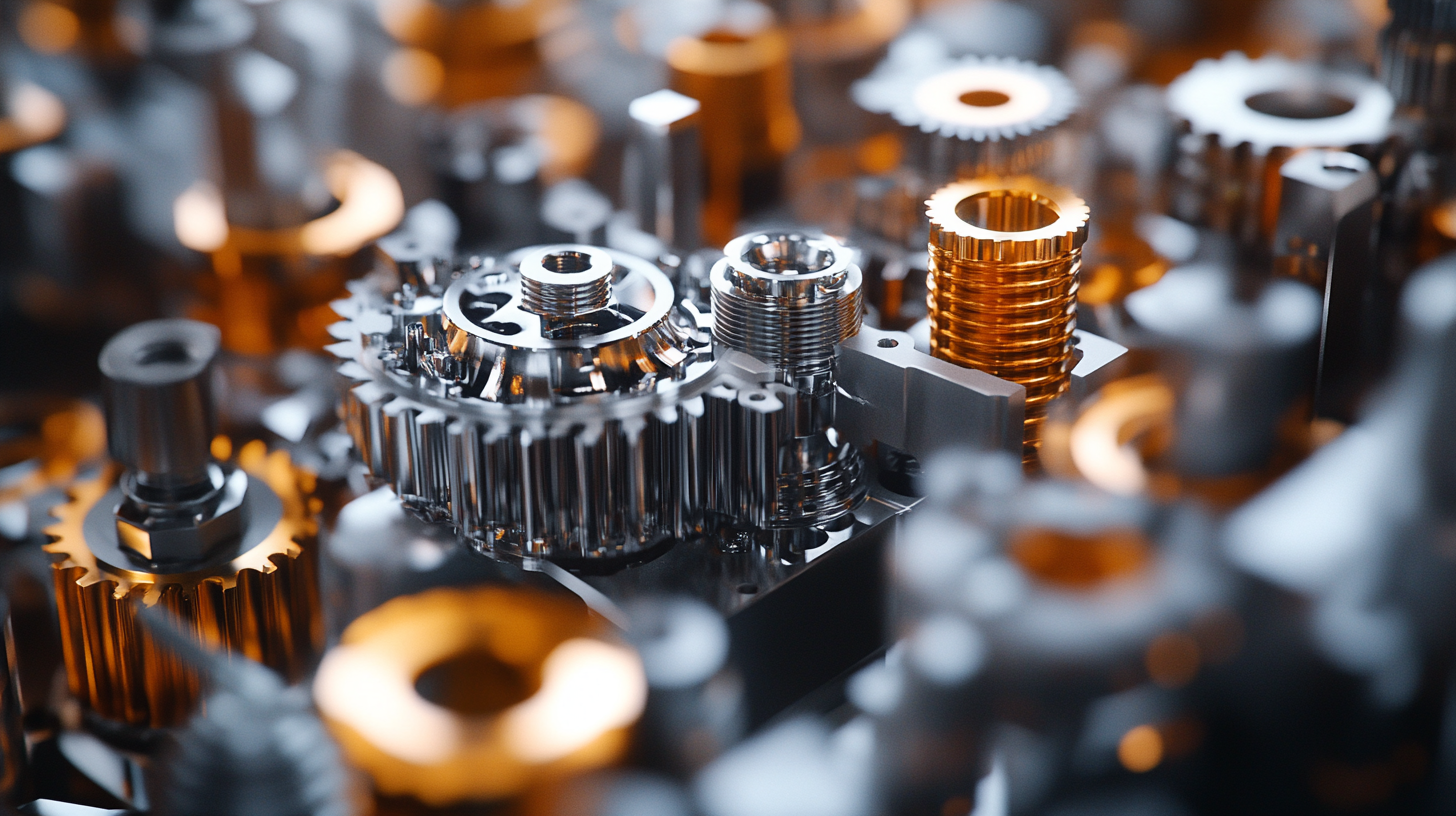
Leveraging Technology: Optimizing Usage of Indexable Tooling in Your Operations
In today’s competitive manufacturing landscape, leveraging technology is crucial for optimizing operations, particularly when it comes to indexable tooling. By adopting advanced software solutions and data analytics, manufacturers can gain deeper insights into tool performance, enabling them to make informed decisions that drive efficiency. This technology helps identify the best tools for specific jobs, reduces downtime, and enhances productivity by ensuring that the right tooling is available when and where it’s needed.
Furthermore, integrating automation with indexable tooling can significantly enhance operational workflows. By automating tool changeovers and monitoring usage in real-time, manufacturers can minimize human error and maximize tool life. This not only improves precision and quality of output but also leads to substantial savings in operational costs. Implementing such technologies ensures that manufacturing processes are not only efficient but also adaptable to changing demands in the market, ultimately leading to improved ROI for global buyers.
5 Essential Tips for Global Buyers: Maximizing ROI with Indexable Tooling in Manufacturing
Tip Number | Tip Description | Expected ROI Impact | Implementation Difficulty |
---|---|---|---|
1 | Identify the Right Indexable Tooling for Your Operations | High | Medium |
2 | Regularly Monitor Tooling Performance | Medium | Low |
3 | Invest in High-Quality Tools | High | Medium |
4 | Train Employees on Tooling Use | Medium | High |
5 | Optimize Inventory Management of Tools | Medium | Low |