Emerging Innovations in Custom Carbide Tooling for 2025 Industry Advancements
As we move towards 2025, the manufacturing industry is on the brink of a technological revolution, one that promises to reshape how we approach tooling and production processes. At the forefront of this transformation is the emergence of innovations in Custom Carbide Tooling. This advanced tooling solution is not just a trend; it represents a significant leap in material science and engineering that caters to the unique needs of various manufacturing sectors. The customization aspect allows for enhanced precision, durability, and efficiency, allowing businesses to optimize their operations and reduce waste.
In this blog, we will explore the latest advancements in Custom Carbide Tooling that are set to make waves in the industry over the next few years. From cutting-edge manufacturing techniques to breakthroughs in design and functionality, these innovations are poised to address the challenges faced by manufacturers today. By understanding these emerging trends, professionals in the field can better prepare for the future, leveraging new technologies to maintain competitive advantage and drive sustainable growth in their operations.
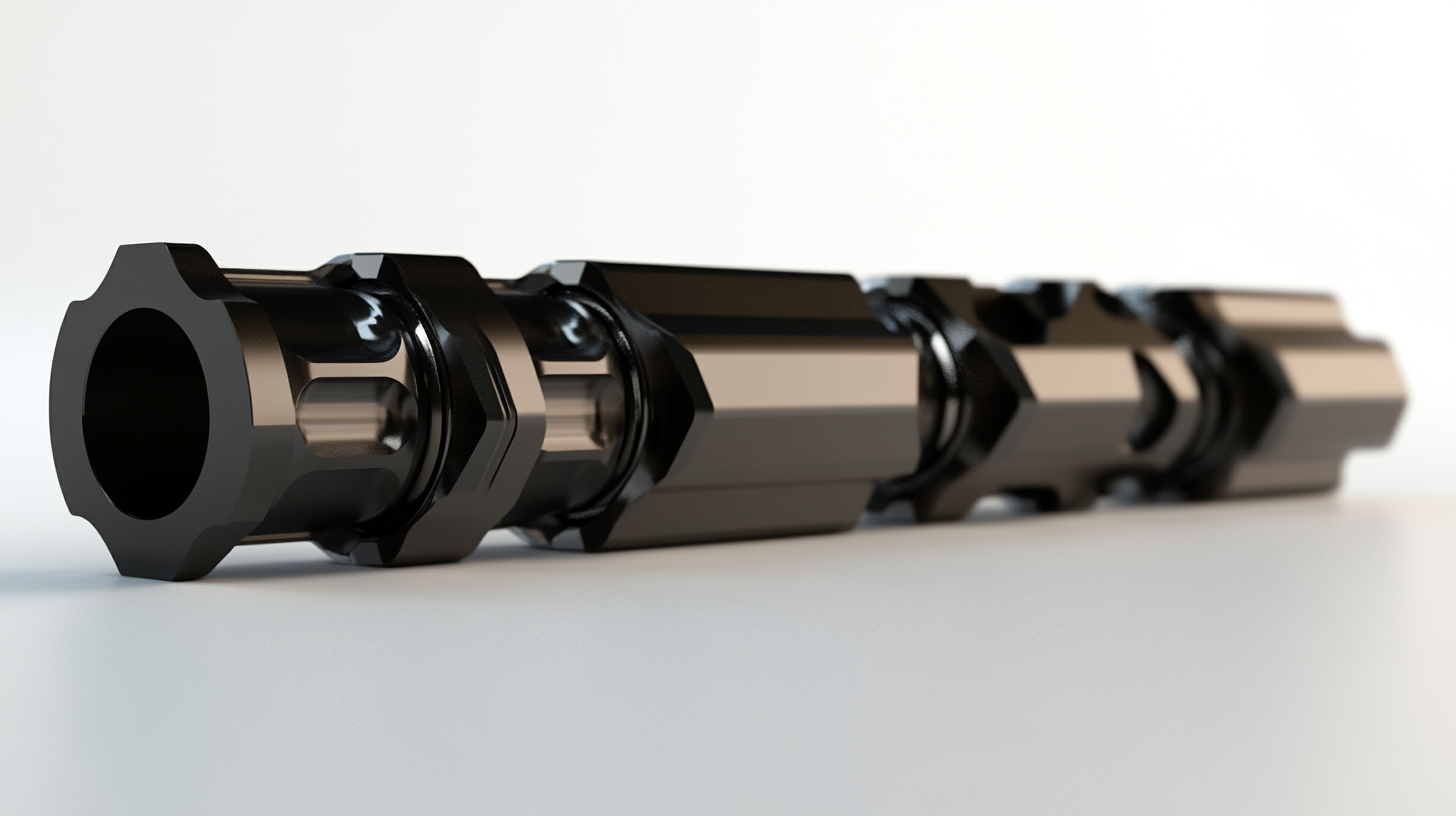
The Future of Custom Carbide Tooling: Key Innovations to Watch
The future of custom carbide tooling is poised for transformation, driven by several key innovations that are set to redefine industry standards by 2025. One of the most significant trends is the integration of advanced materials and coating technologies. According to a report from Market Research Future, the global carbide tools market is expected to reach USD 12 billion by 2026, with a CAGR of 5.2% from 2021. This growth can be attributed to the enhanced durability and performance offered by the latest carbide formulations, which reduce wear and extend tool life significantly. Automation and digitalization are also making waves in the field of custom carbide tooling. By employing AI and machine learning, manufacturers are now able to optimize tool design and production processes. A study from Technavio indicates that the adoption of AI in manufacturing could increase productivity by up to 30% and significantly reduce setup times for custom tooling solutions. This shift towards smart manufacturing not only enhances efficiency but also allows for more tailored solutions that meet specific client needs. Moreover, sustainable practices are becoming a priority in the production of custom carbide tools. Industry leaders are focusing on eco-friendly manufacturing processes and the recycling of materials, aligning with the growing emphasis on environmental responsibility. A report by Mordor Intelligence projects that the sustainable tooling market will generate a revenue of USD 6.75 billion by 2025, as manufacturers strive to minimize their carbon footprint while delivering high-quality products. This convergence of technology, efficiency, and sustainability is setting the stage for a new era in custom carbide tooling, making it one of the most exciting fields to watch in the coming years.
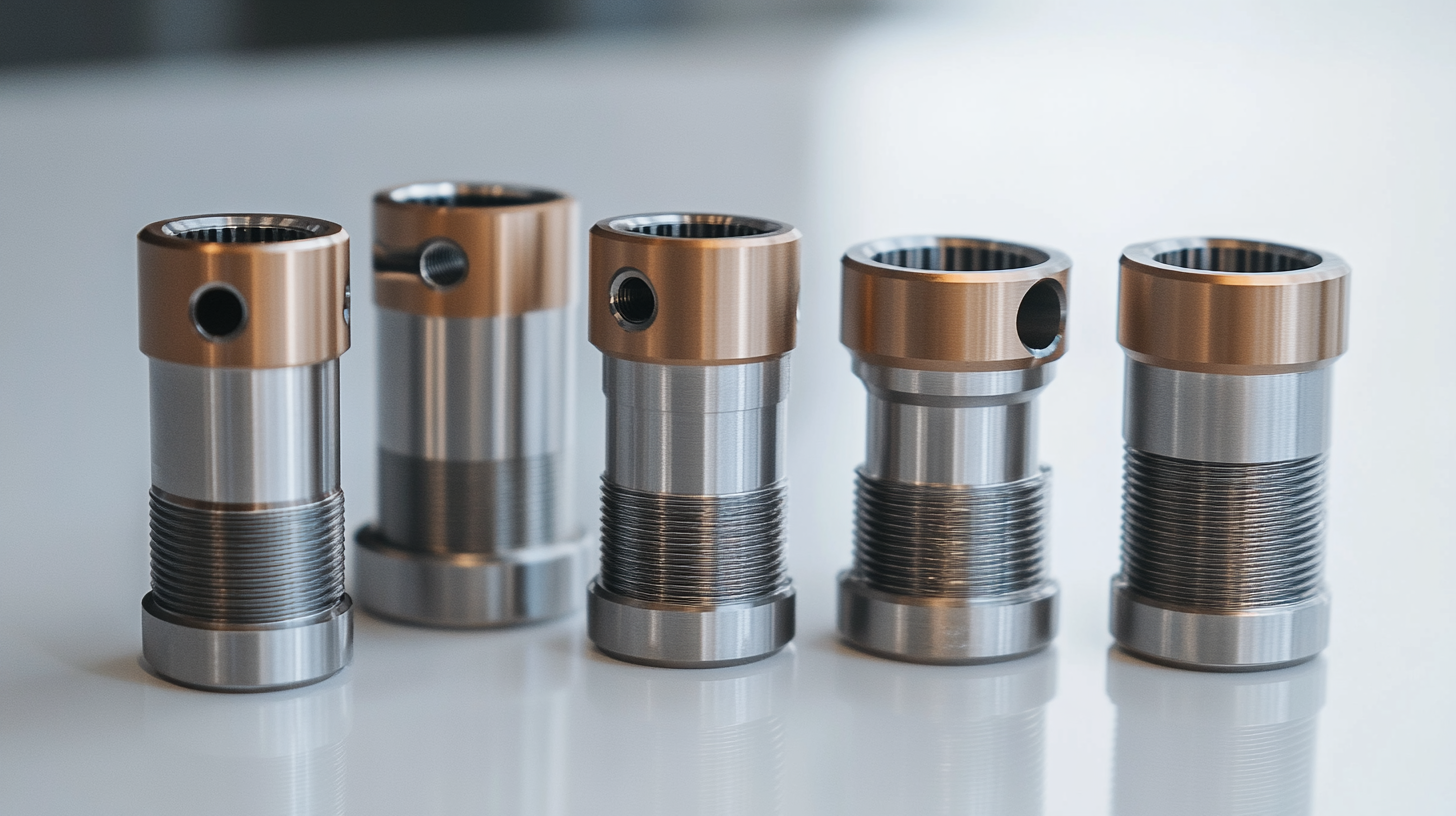
Technological Advancements Driving the Custom Carbide Tooling Market
The landscape of custom carbide tooling is undergoing significant transformation, driven by rapid technological advancements that promise to reshape the industry by 2025. One of the most notable innovations is the increasing accessibility of CVD diamond-coated carbide tools. After years of anticipation, manufacturers are now realizing the potential of these advanced tools, which offer enhanced durability and cutting efficiency, making them highly desirable in demanding applications. This breakthrough could lead to a paradigm shift in manufacturing processes, allowing for greater precision and reduced tool wear.
In parallel, the carbide tools market itself is experiencing robust growth, projected to exceed USD 12.9 billion in 2023, with an anticipated compound annual growth rate (CAGR) of 3.9% through 2032. This upward trend is fueled by heightened demand across various sectors, particularly as industries strive for improved performance and productivity. Additionally, innovations in CNC technology are significantly impacting how cutting tools are designed and produced, streamlining manufacturing processes and enhancing customization capabilities.
Looking towards the future, the synergy between semiconductor advancements and custom carbide tooling cannot be overlooked. As the semiconductor industry advances with trends in power components and advanced packaging, the demand for precision tooling will escalate, further driving innovations in carbide tools. This relationship underscores the importance of adaptability and responsiveness to market needs, positioning custom carbide tooling manufacturers at the forefront of industry innovation and competitiveness.
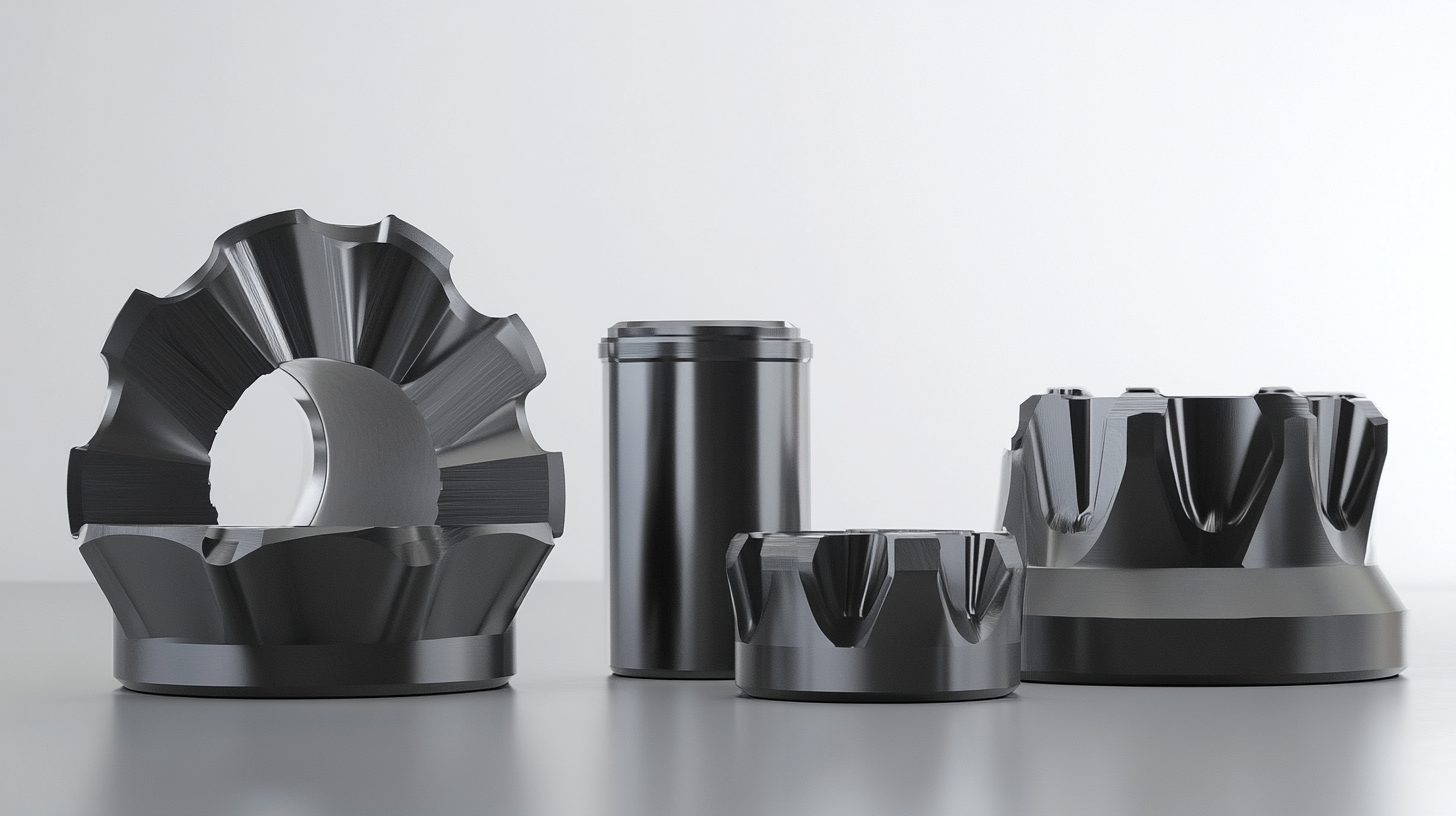
Sustainability Trends in Carbide Tooling Manufacturing for 2025
As the manufacturing industry progresses towards 2025, sustainability is becoming a pivotal focus in carbide tooling production. Companies are realizing that the traditional methods of tooling manufacturing, often associated with high resource consumption and waste generation, need a significant overhaul. In response, innovations in sustainable practices are being integrated into every phase of production, from material sourcing to end-of-life recycling.
One inspiring trend is the shift towards eco-friendly materials that can reduce the environmental impact of carbide tools. Manufacturers are exploring the use of recycled carbide and other sustainable alternatives, which not only lower carbon footprints but also offer comparable performance to conventional materials. This shift not only aligns with global sustainability goals but also meets the growing demand from consumers for greener products, pushing companies to re-evaluate their supply chains and material choices.
Additionally, advances in manufacturing technology, such as additive manufacturing and precision machining, are helping optimize production processes to minimize waste. These techniques allow for better resource management, enabling manufacturers to create more efficient designs that require less material while maintaining strength and longevity. As the industry embraces these sustainable innovations, carbide tooling will not only evolve towards better performance but will also contribute positively to a more sustainable manufacturing ecosystem in 2025 and beyond.

The Role of AI and Machine Learning in Custom Tool Design
As the manufacturing industry progresses into 2025, the integration of artificial intelligence (AI) and machine learning (ML) in custom tooling design is set to revolutionize how tools are developed and utilized. According to a report by MarketsandMarkets, the global AI in manufacturing market is projected to reach $16.7 billion by 2026, growing at a CAGR of 49.5% from 2021. This surge in investment underscores the critical nature of AI and ML technologies in optimizing custom carbide tooling processes.
AI and machine learning algorithms allow for advanced data analysis and predictive modeling, allowing manufacturers to understand and predict tool performance better. For instance, by leveraging large datasets collected from machining operations, AI can identify patterns that lead to tool wear or failure. This process not only enhances the design phase but also enables the creation of tools that are tailored specifically to the unique requirements of complex machining tasks, reducing waste and significantly increasing productivity.
Furthermore, the ability of machine learning systems to continuously adapt improves over time leads to the design of innovative tooling solutions. A recent study by Deloitte suggests that adopting AI in manufacturing operations can lead to a productivity increase of 20-25%. As more companies recognize these advantages, the role of AI and machine learning in custom carbide tooling design will undoubtedly become a cornerstone of competitive advantage in the 2025 landscape.
Challenges and Opportunities in the Evolving Carbide Tooling Landscape
The carbide tooling landscape is witnessing significant transformations as we move toward 2025, bringing both challenges and ample opportunities for innovation. As industries increasingly demand precision and durability, manufacturers are facing the pressure to refine their processes and enhance the performance of their carbide tools. The challenge lies not only in meeting these higher standards but also in adapting to rapidly evolving technologies and market expectations.
One major challenge is the integration of new materials and technologies into existing production lines. As advanced carbide formulations emerge, companies must invest in research and development to ensure compatibility and performance optimization. The move toward sustainable manufacturing processes also adds another layer of complexity. Companies are being urged to minimize waste and energy consumption, which can involve rethinking traditional tooling designs and methods. This transition, while daunting, presents a unique opportunity for innovation and the potential for significant cost savings.
On the other hand, there is a growing opportunity in the field of smart tooling solutions. The adoption of IoT and AI technologies in carbide tooling can lead to enhanced monitoring, predictive maintenance, and improved efficiency. By utilizing data analytics, manufacturers can optimize tool performance and anticipate needs before problems arise. Embracing these technologies not only positions companies as leaders in the market but also contributes to a more responsive and dynamic production environment. The synergy between innovation and adaptation will be essential as we navigate the evolving landscape of carbide tooling in the coming years.