Global Market Trends for Indexable Milling Tools by 2025
The landscape of manufacturing is constantly evolving, and with it comes a growing demand for advanced machining solutions that enhance efficiency and precision. Among these solutions, Indexable Milling Tools have emerged as pivotal components in the toolkit of manufacturers worldwide. These tools offer significant advantages, including increased productivity, reduced downtime, and cost-effectiveness, making them indispensable in various industries. As we approach 2025, understanding the global market trends surrounding Indexable Milling Tools is essential for businesses aiming to stay competitive.
In this blog, we will explore the key trends and innovations that are shaping the future of Indexable Milling Tools. From technological advancements and material developments to shifts in market dynamics, we will analyze the factors driving growth in this sector. Additionally, we will provide insights into emerging applications and the anticipated impact of these trends on manufacturers and suppliers alike. By delving into the intricate landscape of Indexable Milling Tools, we aim to equip industry stakeholders with the knowledge necessary to navigate the upcoming changes and leverage opportunities in the market.
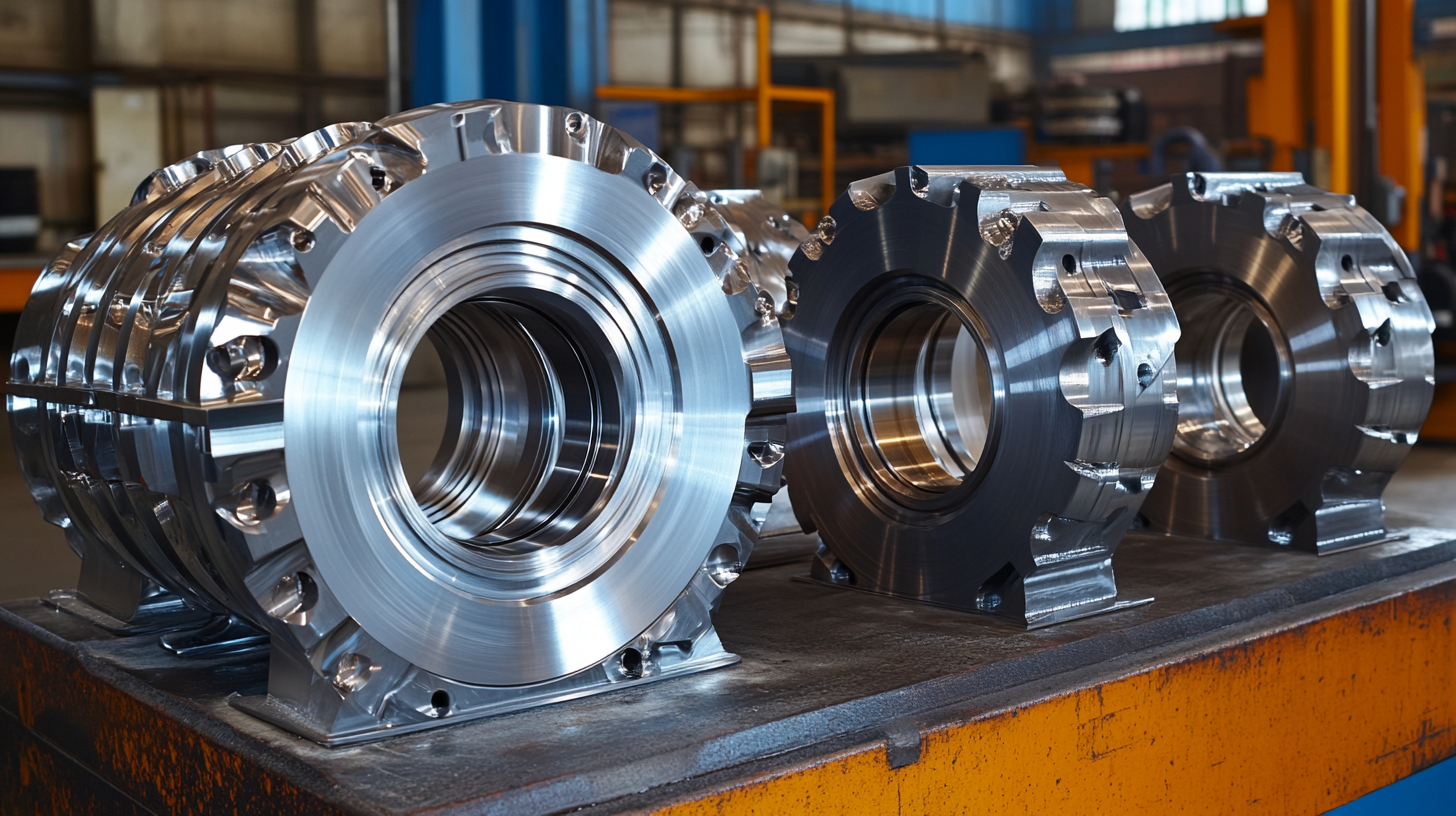
Emerging Technologies Driving Innovation in Indexable Milling Tools
The evolution of indexable milling tools is poised for significant advancement by 2025, driven by a variety of emerging technologies that are reshaping the manufacturing landscape. One of the primary innovations influencing this sector is the integration of artificial intelligence (AI) and machine learning. These technologies enable manufacturers to optimize cutting processes and predict tool wear, thereby improving efficiency and reducing downtime. By leveraging data analytics, companies can analyze machining parameters in real-time, allowing for smarter decision-making and enhanced production capabilities. Additionally, the rise of advanced materials, such as coated carbide and ceramic composites, is enhancing the performance and durability of indexable milling tools. These materials not only increase the lifespan of tools but also enable machining of harder materials with greater precision. Furthermore, developments in additive manufacturing are paving the way for the creation of complex geometries in tooling, providing a customized approach to meet specific machining needs. As these technologies continue to evolve, they are expected to drive increased collaboration across the manufacturing sector, fostering innovation and improving overall productivity. Sustainability is another critical area in which emerging technologies are making an impact. The focus on environmentally friendly processes is prompting manufacturers to develop more eco-conscious milling tools. Innovations in recycling and tool reconditioning processes are set to revolutionize the lifecycle management of tools, reducing waste and promoting a circular economy within the industry. As such, the future of indexable milling tools not only promises enhanced performance but also a commitment to sustainable practices that align with global environmental goals.
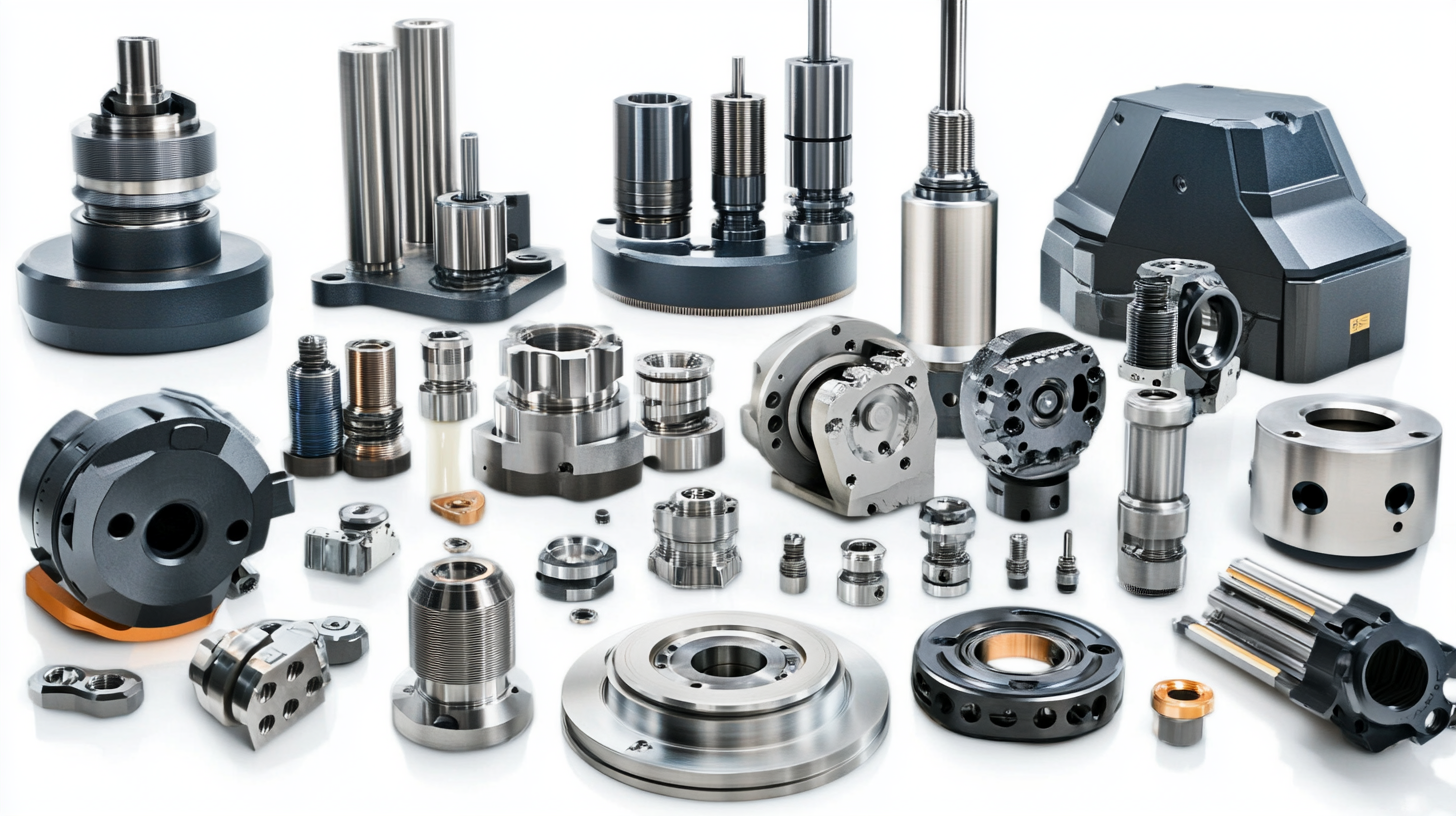
Market Demand Analysis for Indexable Milling Tools in Various Industries
The demand for indexable milling tools is witnessing a significant surge across various industries, driven by the need for precision and efficiency in machining processes. Industries such as aerospace, automotive, and manufacturing are increasingly adopting these tools due to their versatility and cost-effectiveness. As these sectors continue to innovate and expand, the requirement for advanced milling solutions that can handle complex materials and intricate designs becomes paramount.
In the aerospace sector, the demand for lightweight yet durable components is pushing manufacturers to seek out indexable milling tools that can effectively machine advanced materials, including composites and titanium alloys. These tools offer the precision necessary to meet stringent aerospace standards while ensuring reduced manufacturing times. Similarly, the automotive industry is experiencing a shift towards electric vehicles, which require specialized components. Indexable milling tools are essential in producing high-quality parts with improved accuracy, contributing to the overall performance and sustainability of new vehicle models.
Moreover, the shift toward digital manufacturing practices, including automation and smart factories, plays a crucial role in the rising demand for indexable milling tools. The integration of robotics and advanced software in the manufacturing process enhances productivity and reduces errors, making indexable tools an essential component for manufacturers looking to stay competitive. As these trends evolve, the market for indexable milling tools is poised for substantial growth by 2025, reflecting the changing needs and technological advancements in various industries.
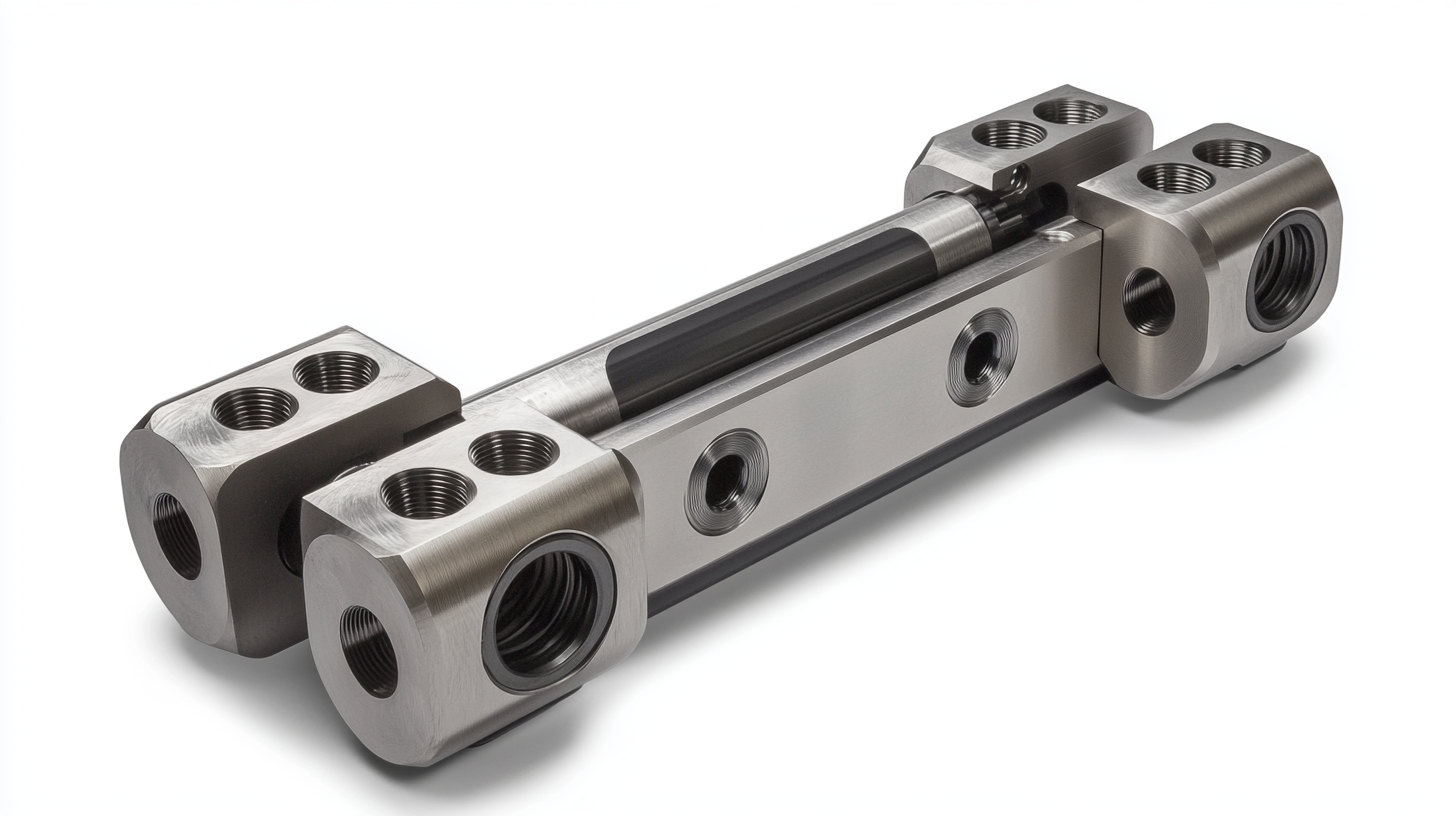
Regional Insights: Growth Opportunities in Global Markets
The global market for indexable milling tools is poised for significant growth by 2025, with various regions presenting unique opportunities and challenges. In Asia-Pacific, robust industrial growth and the expansion of manufacturing hubs, particularly in countries like China and India, are driving demand for advanced milling tools. The rising emphasis on precision engineering and automation in these regions will likely boost the market, leading to increased adoption of innovative tooling solutions that enhance productivity and efficiency.
Meanwhile, North America is expected to experience a steady growth trajectory, primarily due to technological advancements and a strong focus on R&D within the manufacturing sector. The presence of established automotive and aerospace industries further solidifies the demand for efficient milling tools tailored to meet the specific requirements of high-performance applications. Companies operating in this region should prioritize local strategies that address unique market dynamics and consumer preferences.
In Europe, the push for sustainability and eco-friendly manufacturing processes is reshaping the landscape for indexable milling tools. Manufacturers are increasingly seeking tools that not only deliver high performance but also minimize environmental impact. This region represents a significant opportunity for innovation, particularly in the development of biodegradable and recyclable tooling options. By aligning product offerings with regional regulatory requirements and sustainability goals, companies can capture a larger market share in this evolving sector.
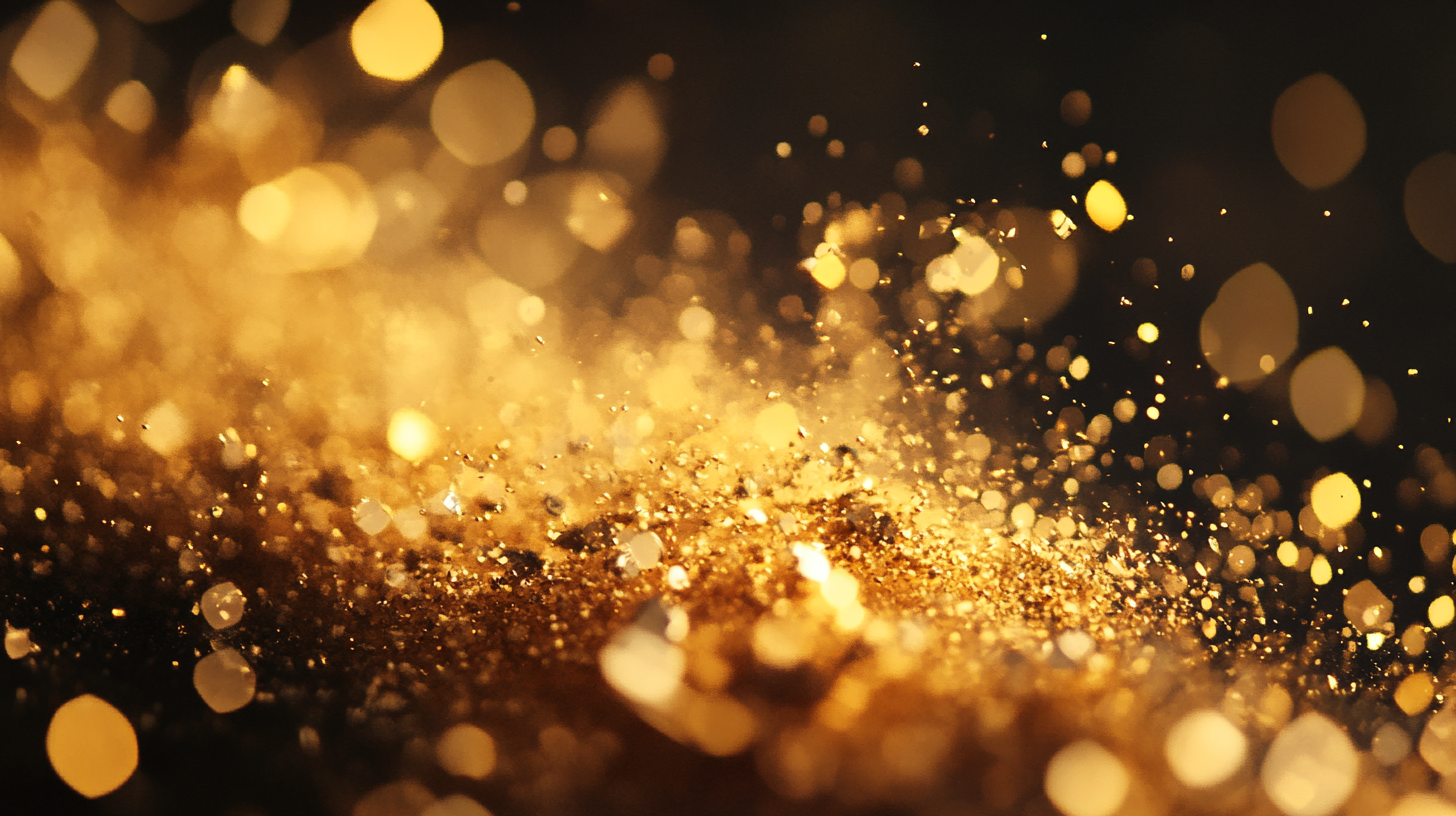
Sustainability Trends Impacting the Indexable Milling Tools Sector
The indexable milling tools sector is undergoing significant changes as sustainability trends become increasingly central to market dynamics. Manufacturers are exploring eco-friendly materials and production processes aimed at reducing waste and energy consumption. Innovations such as ceramic and high-speed steel tools designed for longevity help minimize tooling waste over time. This shift not only aligns with global sustainability goals but also enhances business competitiveness by appealing to environmentally conscious consumers.
Additionally, companies are implementing circular economy principles, focusing on recycling and reusing materials in tool production. More organizations are adopting sustainable practices, such as reclaiming used tools and grinding them for reuse, which not only extends product lifecycles but also decreases resource consumption. This commitment to sustainability is transforming how manufacturers operate, driving them to invest in technologies that support efficient production methods while minimizing their carbon footprint.
As the demand for sustainable practices grows, the indexable milling tools market is likely to see increased regulatory pressures and consumer demands for transparency. This evolution will challenge businesses to adapt swiftly, implementing sustainable solutions that resonate with their values while meeting the needs of a modern, conscious market. Ultimately, these sustainability trends are poised to shape the future landscape of the indexable milling tools industry by 2025 and beyond.
Future Forecast: Predictions for Indexable Milling Tools by 2025
As we look toward 2025, the landscape of indexable milling tools is poised for significant transformation driven by technological advancements and shifting market dynamics. According to a recent report from Research and Markets, the global indexable milling tools market is projected to reach approximately $11 billion by 2025, growing at a compound annual growth rate (CAGR) of around 6.5% from 2020. The increasing demand for precision machining in industries such as aerospace, automotive, and manufacturing is a primary catalyst for this growth.
One of the key trends shaping the indexable milling tools market is the rise in the adoption of automation and smart manufacturing technologies. Industry players are increasingly investing in digital solutions such as IoT integration, which enables real-time data monitoring and enhances operational efficiency. Furthermore, advancements in tool coating technologies are expected to improve tool life and performance, making them more appealing to manufacturers looking to maximize productivity while minimizing costs. As highlighted in a study by Mordor Intelligence, innovations in carbide and ceramic materials are set to boost the performance capabilities of indexable milling tools, catering to a wider range of applications.
Additionally, the Asian market, particularly countries like China and India, is anticipated to witness substantial growth due to their rapid industrialization and expansion of the manufacturing sector. The International Trade Administration reports that the rise of the middle class and increased foreign investments are driving demand for advanced machining tools, which bodes well for indexable milling tool manufacturers aiming to expand their market presence.
Overall, as these trends continue to develop, the market for indexable milling tools by 2025 will not only reflect growth in terms of revenue but also a shift towards smarter, more efficient manufacturing practices that align with the future of industrial operations.