Key Factors in Selecting Reliable Manufacturers for Indexable Tool Repair Services
Today’s manufacturing world is really competitive, and if you want to stay ahead, it’s all about how well your machining tools perform and how long they last. A recent report from the National Tooling and Machining Association (NTMA) threw out some eye-opening stats: around 30% of a company's manufacturing expenses are tied up in tooling. So, it’s pretty clear that keeping those tools in tip-top shape is super important. That’s where Indexable Tool Repair services come into play—they’re a game changer for stretching out tool life while cutting down on those pesky downtime moments and production hiccups. If companies can tap into solid repair services, they really can streamline their processes and save a chunk of change that would otherwise go toward replacing tools.
Now, choosing the right manufacturer for Indexable Tool Repair isn’t just a walk in the park. A report from the Society of Manufacturing Engineers (SME) pointed out that businesses that partner with top-notch service providers see an impressive 20% boost in tool performance, plus they get faster repair times. So, getting a grip on what really matters when picking a repair partner is key for anyone looking to ramp up their productivity. In this blog post, we’re going to dive deep into those key factors, giving you some solid tips for finding trustworthy manufacturers that can help with your indexable tool repair needs.
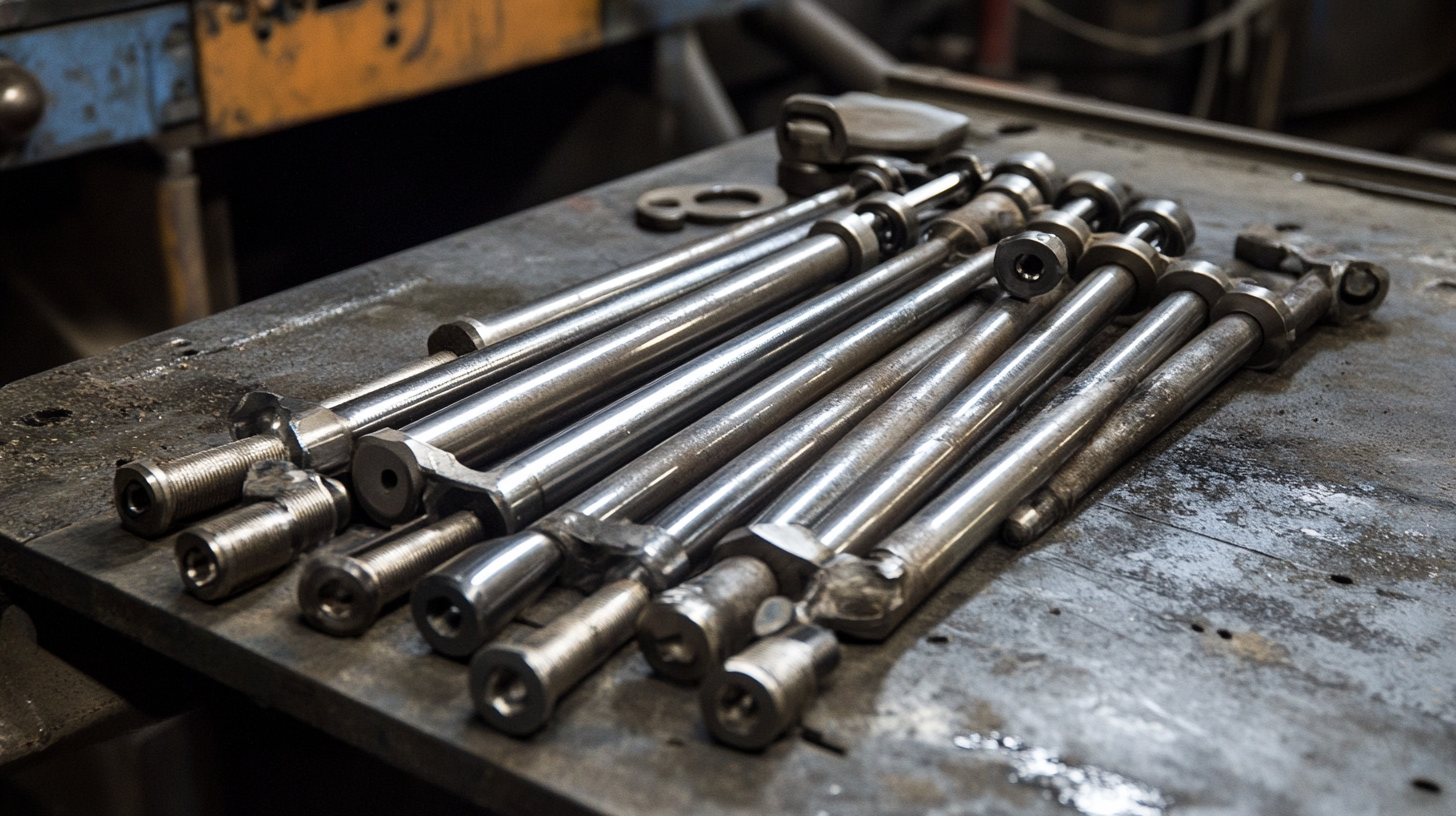
Identifying Essential Qualities in Tool Repair Service Providers
Looking for reliable manufacturers for indexable tool repair services? It’s super important to pinpoint the key qualities that really make the best service providers shine. You want to find those who have a solid reputation for quality and dependability. These traits show how well they can keep those precision tools running smoothly. Taking a deep dive into customer reviews and checking their industry certifications can give you some great insights into just how credible they are and what their track record looks like. One big thing to consider is the technical know-how of their repair staff. With all the complexities of modern tooling systems, it’s crucial that they really get advanced diagnostic solutions. Just a quick note—the motorcycle diagnostic scanning tool market is booming! By 2024, it's set to surpass $1.5 billion, thanks to the growing demand for sophisticated ECU and sensor-based systems. So, it only makes sense that tool repair services need to keep pace with these tech advancements to stay effective and competitive. Let’s not forget about having cutting-edge repair equipment and technologies. Manufacturers that put their money into top-notch tools and systems are in a way better position to provide precise repairs. This means better performance and a longer lifespan for the tools. With the motorcycle diagnostic tool market expected to grow at a healthy rate of 6.2% from 2025 to 2034, it’s clear that embracing innovative solutions is going to be key for any service provider wanting to thrive in this ever-evolving tool repair landscape.
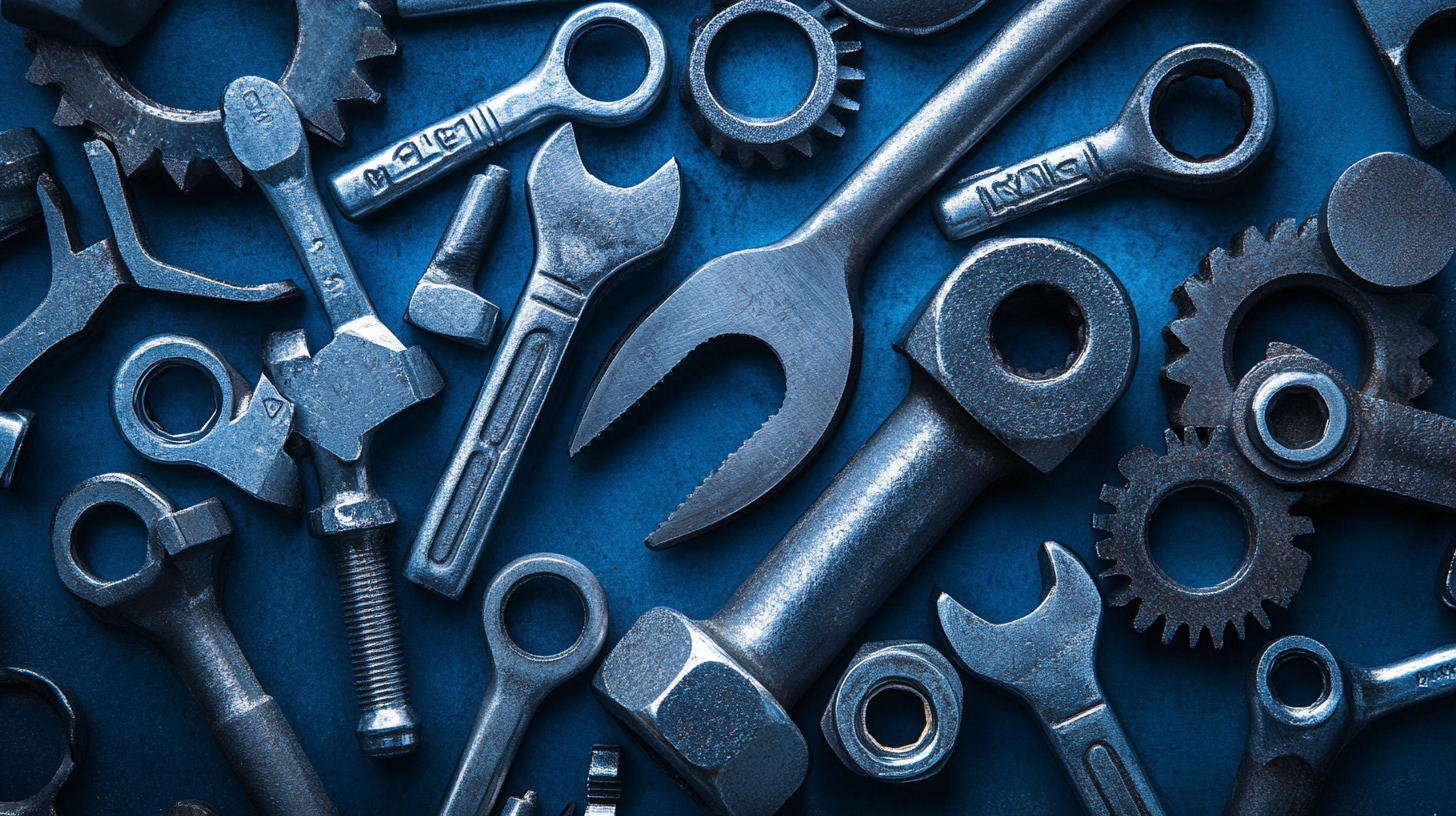
Evaluating Manufacturer Reputation and Industry Experience
So, when you're on the hunt for a trustworthy manufacturer for indexable tool repair services, one of the biggest things to keep in mind is their reputation and how long they’ve been in the industry. As things change and evolve, having a solid reputation is super important for building trust and credibility. I came across some reports recently that said sectors like finance are really stepping up their game when it comes to managing reputation risks. You know, the frameworks that regulatory bodies put in place really show how a company’s standing in the market can impact everything from operations to client relationships.
Now, when it comes to tool repair services, you can usually tell a lot about a manufacturer by how long they've been around. Companies that have been in the game for years—sometimes even decades—usually have a wealth of knowledge and skills that newer players might not have yet. Research has shown that these established manufacturers don’t just get higher customer satisfaction; they also tend to have stronger relationships with their suppliers, which often leads to better service.
And let’s not forget about professional integrity and accountability. There’s been a recent push in the securities industry for promoting compliance and professionalism, and it’s just as important for tool repair manufacturers to show they have these values too. A company that’s committed to ethical practices and sticks to industry standards is far more likely to offer reliable and consistent service.
In short, checking out a manufacturer’s reputation and experience in the industry is key when choosing a partner for indexable tool repair services. It's important for businesses to look at both the numbers—like years in service—and some of the less tangible stuff, like ethical behavior and feedback from customers. Taking this well-rounded approach can really help in finding a manufacturer that vibes well with your company’s values and needs.
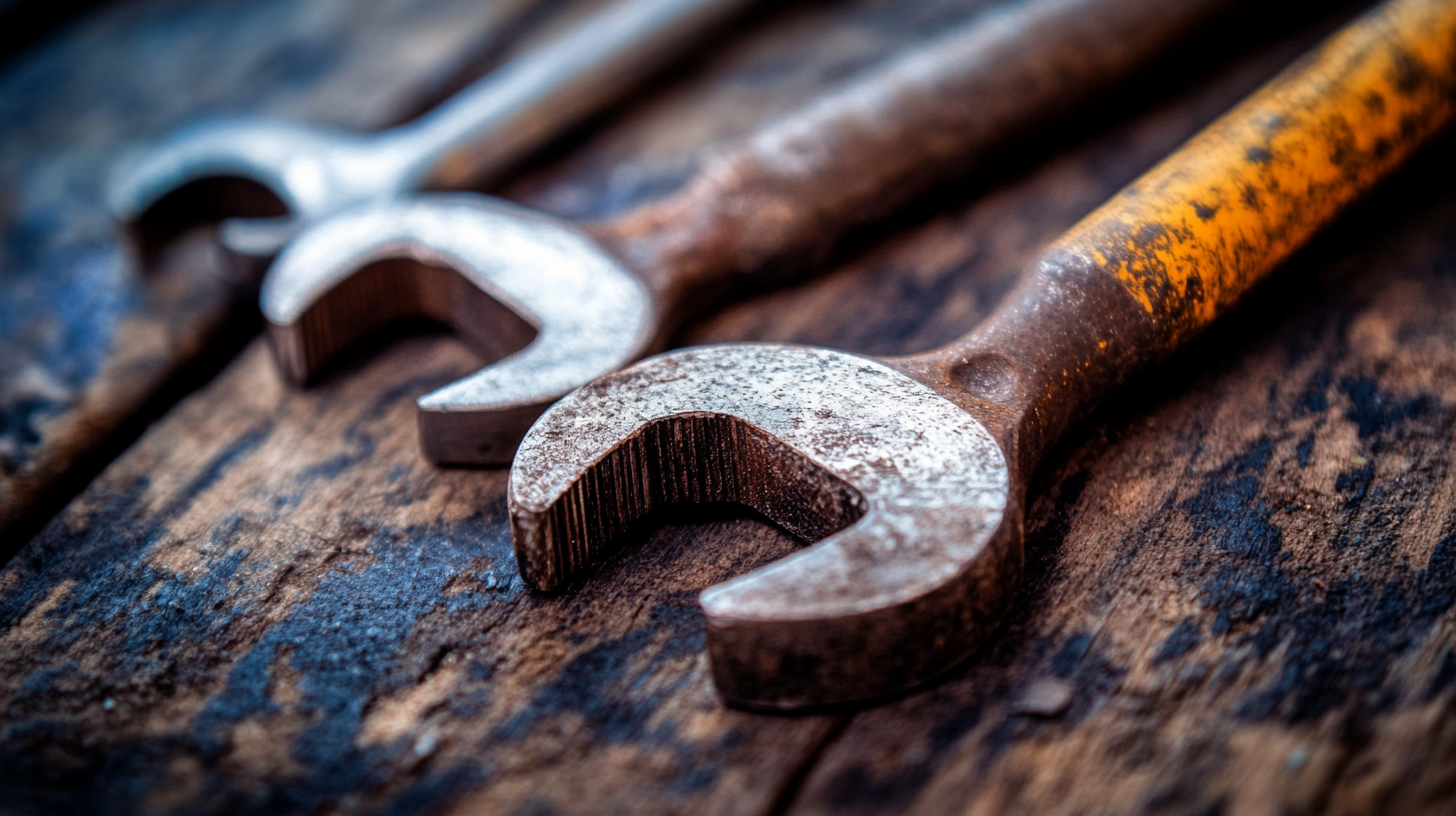
Assessing Quality Control Measures and Repair Standards
So, when you're on the hunt for trustworthy manufacturers to handle indexable tool repairs, it’s super important to take a good look at their quality control measures and repair standards. I recently came across a report from the International Organization for Standardization (ISO), and it really drives home the point that sticking to tough quality standards is key for making sure those tools perform well and last long. In today’s competitive market, the manufacturers that really nail down strict quality control processes are the ones that see fewer defects and keep their customers coming back for more. And hey, this fits right in with the new Quality Country Construction Outline that’s been put out by the authorities, emphasizing how crucial quality is in manufacturing practices all across the country.
On top of that, we can’t overlook the economic side of things when it comes to keeping those repair standards high. There’s this analysis from a well-known industry consultancy that found tools cared for under high standards can actually last 30% longer than those that don’t get as much attention. This not only cuts down on the need to replace tools regularly but also helps businesses run smoother and manage costs better.
And let’s not forget, it’s really important for manufacturers and service providers to keep a continuous feedback loop going. That way, they can make sure their quality control measures evolve along with industry standards and what customers expect. This proactive approach plays a crucial role in building a solid reputation in the repair services market. So, it’s really essential for everyone involved to keep quality at the forefront of all that they do.
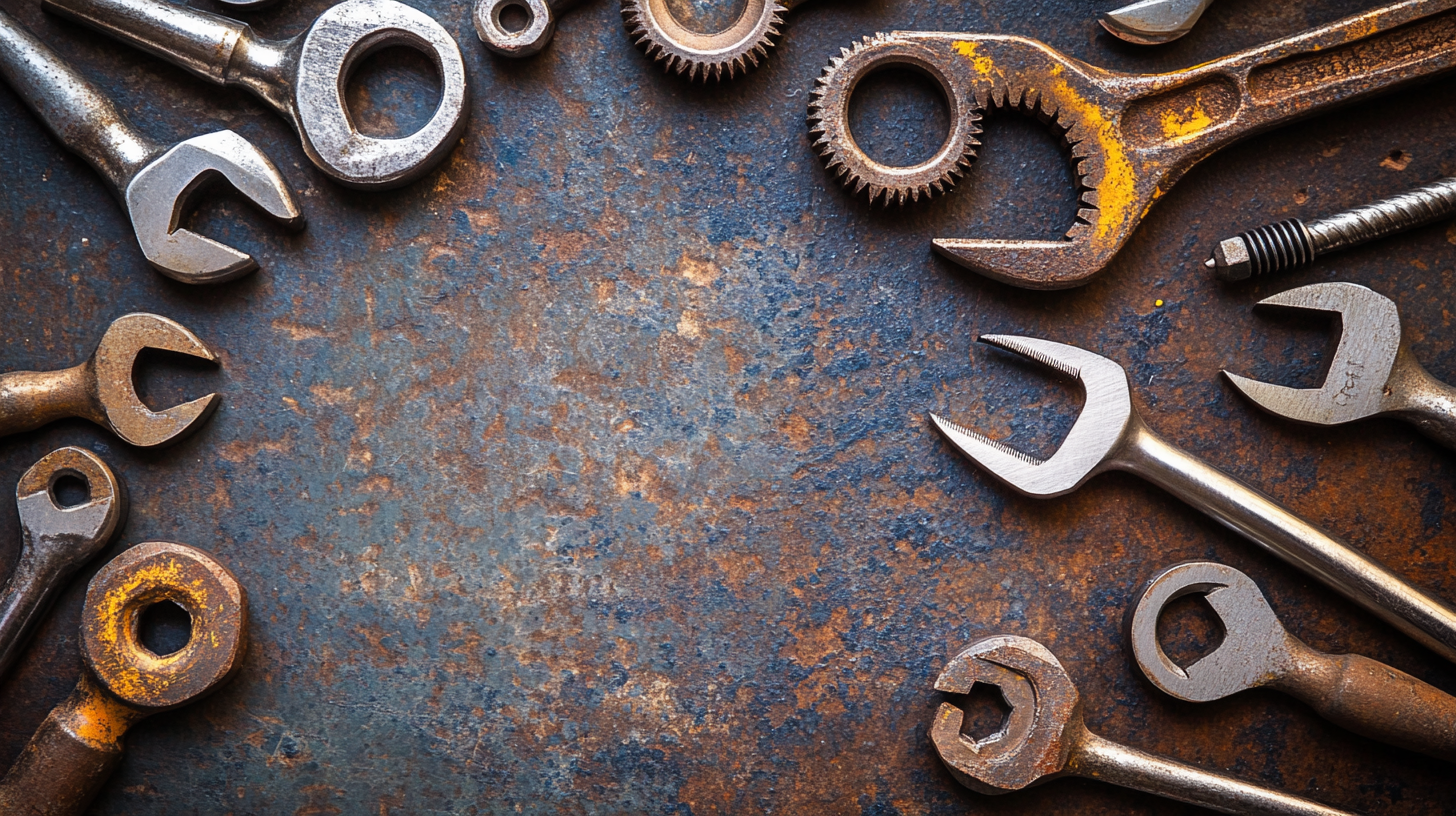
Understanding Cost Structures and Value in Tool Repair
So, when you're on the hunt for dependable manufacturers for indexable tool repair services, it really pays to get a grip on how their pricing works and what kind of value they’re offering. At first glance, that initial quote for repairs might look really good, but you gotta dig a bit deeper to see what's actually included in that number. Different manufacturers have their own ways of charging; some might give you a flat rate for repairs, while others take into account how complex the service is or what specific tool they're fixing. Knowing this helps you pick a manufacturer that not only fits your budget but also meets the quality standards you need for your tools to really perform well.
And here's the thing: value in tool repair isn’t just about staring at the price tag. Sometimes, a pricier service can lead to tools that last longer and work better, which means you won’t be sending them in for repairs nearly as often. So, it’s super important to think about the manufacturer’s reputation, their know-how with the specific tools you need, and whether they back up their work with a solid warranty. Those manufacturers who really care about quality service can save you some cash in the long run, thanks to less downtime and smoother operations. Bottom line? Taking a closer look at cost versus value is crucial for making a smart choice when you're picking a reliable tool repair service.
Exploring Customer Support and After-Service Reliability
Choosing a dependable manufacturer for indexable tool repairs? Well, a big thing to consider is their customer support and how reliable they are afterward. You know, having a customer support team that’s quick to respond can really make your whole repair experience so much smoother. It’s super important to see how easily you can get in touch with them for any inquiries or concerns you might have. A manufacturer that provides several ways to communicate—like phone, email, or even live chat—shows they genuinely care about keeping their clients happy. Plus, how fast and helpful they are in their responses can tell you a lot about how much they value their customers’ needs.
Now, let’s talk about after-service reliability, which is just as crucial. A trustworthy manufacturer should really stand behind the longevity and performance of their repaired tools. You’ll want to ask about warranties and guarantees on those repairs, just to make sure you won’t end up dealing with the same issues right after service. It’s a good sign if they also check in on you after the service is done to see how the tools are holding up. That kind of follow-up shows just how dedicated they are to keeping their quality standards high and building strong relationships with clients. It’s this commitment that can give you peace of mind and really solidify your trust in what they do.
In today’s competitive world, businesses that shine in customer support and after-service reliability tend to rise above the rest. By focusing on these aspects, you can be sure you're teaming up with a manufacturer that not only has the technical stuff down but is also there to help you hit your operational goals. So, when you’re checking out potential manufacturers, it’s smart to go beyond just their tech skills and think about the overall experience they provide through their customer service.