Unlocking the Potential of Carbide Cutters for Precision Manufacturing Needs
In the ever-evolving landscape of precision manufacturing, the demand for high-performance tools is paramount. One such tool that has garnered significant attention is the carbide cutter. Renowned for its exceptional durability and precision, a carbide cutter is an indispensable asset for manufacturers aiming to achieve intricate designs and flawless finishes. The properties of carbide, including its hardness and resistance to wear, make it ideal for a variety of applications, from machining to fabrication. As industries continue to push the boundaries of production demands, understanding how to maximize the potential of carbide cutters is crucial. This blog delves into the benefits, applications, and best practices for utilizing carbide cutters effectively, illuminating their pivotal role in enhancing manufacturing efficiency and precision.
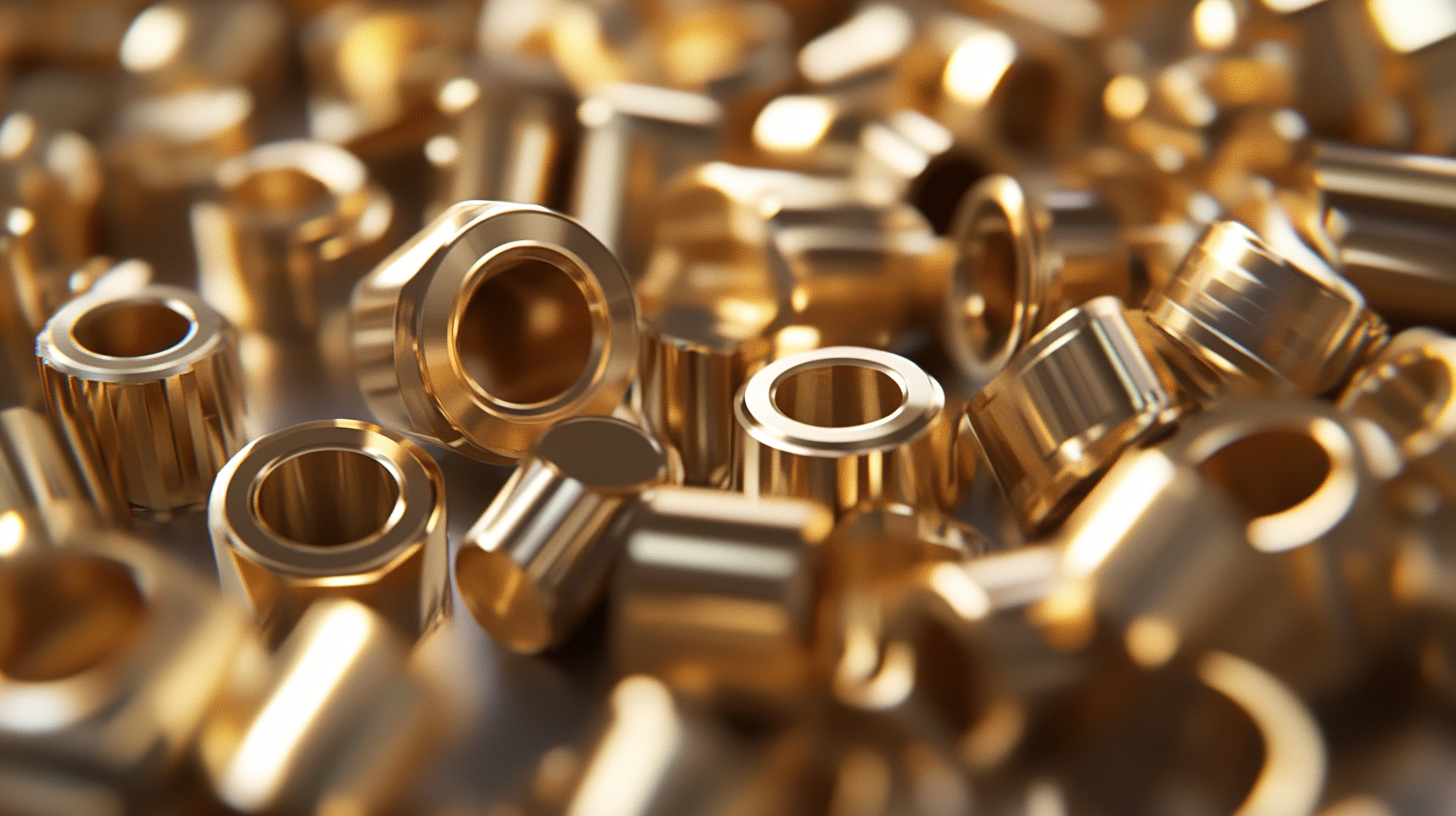
Understanding the Unique Properties of Carbide Cutters in Precision Manufacturing
Carbide cutters have emerged as indispensable tools in the realm of precision manufacturing, owing to their unique properties that enhance productivity and accuracy. Unlike conventional steel cutters, carbide materials consist of high-density tungsten carbide, which offers superior hardness and wear resistance. This results in prolonged tool life and the ability to withstand high cutting speeds, making them ideal for a variety of applications, from automotive parts to intricate aerospace components. The ability of carbide cutters to maintain sharp edges even under extreme conditions allows manufacturers to achieve the tight tolerances necessary for modern engineering standards.
Moreover, the versatility of carbide cutters cannot be overstated. They come in various shapes and sizes, designed for specific tasks such as milling, drilling, or grinding. This adaptability, combined with their inherent thermal stability, allows manufacturers to tackle a wide range of materials, from softer metals to hard alloys. In addition, the unique composition of carbide helps dissipate heat generated during cutting, preventing tool degradation and improving overall machining efficiency. As precision manufacturing continues to evolve, the role of carbide cutters as a cornerstone for achieving high-quality results is becoming increasingly significant.
Unlocking the Potential of Carbide Cutters for Precision Manufacturing Needs
This chart illustrates the unique properties of carbide cutters and their effectiveness in precision manufacturing applications. The data showcases the performance of different carbide cutter types based on factors such as hardness, wear resistance, and cutting speed.
Key Advantages of Using Carbide Cutters Over Traditional Cutting Tools
Carbide cutters have emerged as a game changer in precision manufacturing, offering advantages that surpass traditional cutting tools. According to the 2022 Metal Cutting Trends Report by Research and Markets, carbide tools can last up to 10 times longer than high-speed steel (HSS) tools, reducing the frequency of tool changes and downtime. This longer lifespan not only increases productivity but also translates into significant cost savings for manufacturers. The report also highlights that carbide cutters, due to their hardness and thermal stability, can be operated at higher speeds, achieving better surface finishes and tighter tolerances in machining processes.
When choosing carbide cutters, it's essential to consider the specific application requirements. Tips for maximizing the benefits of carbide tooling include selecting the appropriate grade based on material compatibility and ensuring proper coolant usage to minimize heat build-up during cutting. Additionally, adopting a systematic maintenance routine can enhance the longevity of carbide tools, minimizing wear and maintaining their effective performance.
Furthermore, carbide's resistance to abrasion and deformation makes it a superior choice for manufacturing complex geometries and components in demanding industries like aerospace and automotive. As manufacturers continue to seek out efficiency and quality, the transition from traditional cutting tools to carbide options is likely to accelerate, propelling forward the capabilities of precision machining.
Advantages of Using Carbide Cutters in Precision Manufacturing
Applications of Carbide Cutters in Various Manufacturing Industries
Carbide cutters are revolutionizing precision manufacturing across multiple industries due to their durability and efficiency. According to a report by Smithers Pira, the global market for carbide cutting tools is projected to reach $18 billion by 2025, driven by increasing demand in sectors such as automotive, aerospace, and electronics. These tools provide superior hardness and wear resistance compared to traditional materials, enabling manufacturers to achieve tighter tolerances and extended tool life, which are critical in high-speed machining processes.
In the automotive industry, carbide cutters are essential for producing complex engine components with high precision. A study by the National Institute of Standards and Technology (NIST) highlights that the use of carbide tools has improved the dimensional accuracy of automotive parts by 30%, reducing waste and production costs. Similarly, in the aerospace sector, carbide cutters facilitate the machining of advanced alloys and composite materials that are increasingly used in aircraft. This high-performance tooling not only enhances the profit margins but also allows for the production of lighter, more fuel-efficient aircraft, aligning with current trends towards sustainability in manufacturing.
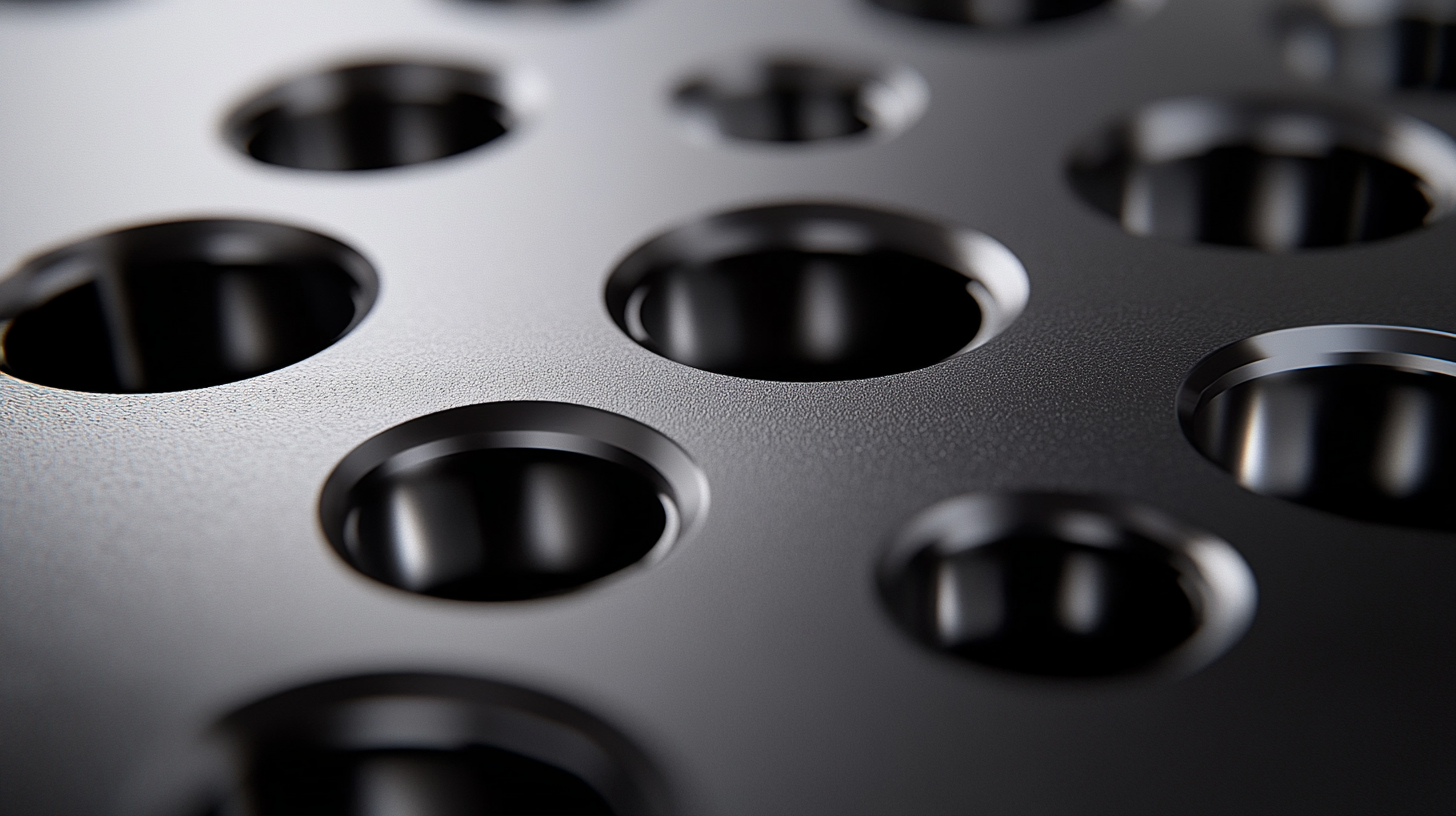
Selecting the Right Carbide Cutter for Your Precision Manufacturing Needs
When it comes to precision manufacturing, selecting the right carbide cutter is crucial for achieving the desired accuracy and efficiency in production. Carbide cutters are renowned for their durability and ability to maintain sharpness over extended periods, making them the go-to choice for demanding machining tasks. However, not all carbide cutters are created equal; understanding the specific requirements of your manufacturing process is essential for making an informed choice.
First, consider the material you will be working with. Different carbide cutter geometries and coating options are designed for various materials, whether it's aluminum, steel, or tougher composites. Look for cutters with the right tip geometry that can enhance chip removal and reduce friction, leading to improved surface finishes. Additionally, assess the cutter's diameter and length, as these factors can significantly influence your machining capabilities and the precision of cuts. By aligning the cutter specifications with your manufacturing needs, you can ensure optimal performance and longevity of your tools, ultimately saving time and resources in production.
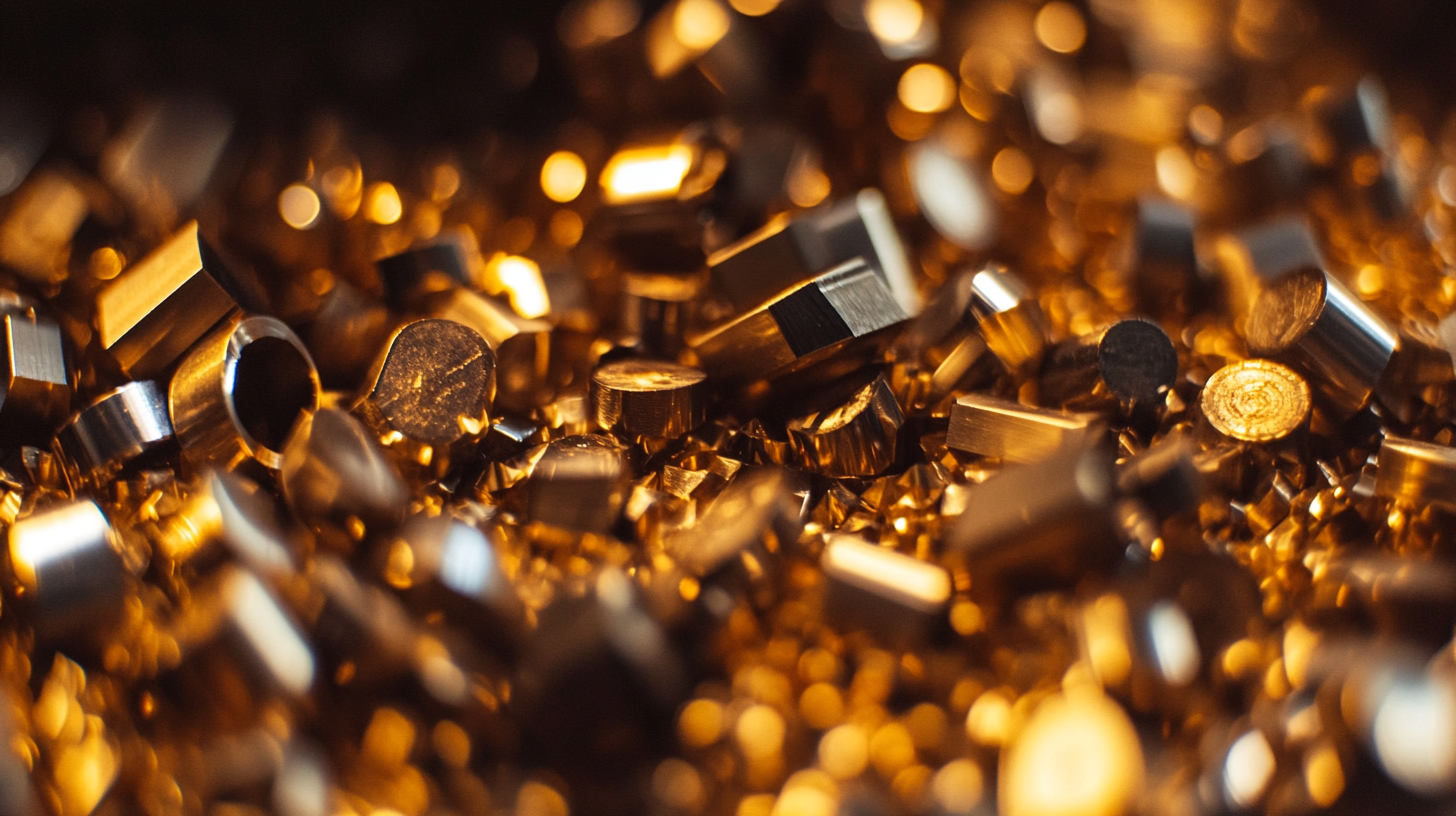
Maintenance Tips to Enhance the Longevity of Carbide Cutters in Production
Carbide cutters have become indispensable tools in precision manufacturing, offering superior performance and durability. To maximize their effectiveness in production, proper maintenance is essential. One of the key strategies for extending the life of carbide cutters is regular sharpening. Keeping the cutting edges honed ensures optimal cutting performance, reduces the risk of tool breakage, and improves overall product quality.
Another crucial maintenance tip is to ensure proper storage. Carbide cutters should be kept in a dry and clean environment, away from moisture and contaminants that could lead to corrosion. Using a dedicated storage solution can prevent physical damage and preserve the integrity of the cutting edges. Moreover, when using these tools, it’s vital to adhere to the recommended feed rates and speeds to minimize wear and tear while achieving the best results in manufacturing.
Implementing these maintenance practices will not only extend the longevity of carbide cutters but also enhance their performance, leading to improved productivity in manufacturing processes. Regular checks and a proactive approach to maintenance can significantly impact operational efficiency.
Unlocking the Potential of Carbide Cutters for Precision Manufacturing Needs - Maintenance Tips to Enhance the Longevity of Carbide Cutters in Production
Maintenance Tips | Frequency | Expected Impact | Additional Notes |
---|---|---|---|
Proper Cleaning | After each use | Reduces wear and tear | Use a soft brush |
Proper Storage | Always | Prevents chipping | Use protective cases |
Regular Inspection | Weekly | Identifies damage early | Look for signs of wear |
Sharpening | As needed | Improves cutting efficiency | Consult a professional |
Cooling Techniques | During operation | Prevents overheating | Use appropriate coolant |