Maximizing Efficiency in Manufacturing with Production Tools and Best Practices for Implementation
In today's rapidly evolving manufacturing landscape, maximizing efficiency is more crucial than ever. The adoption of advanced production tools has transformed the way companies operate, allowing them to streamline processes, reduce waste, and improve overall productivity. By harnessing the power of these tools, manufacturers can not only enhance their output quality but also adapt to changing market demands with greater agility. This blog explores various production tools that can be integrated into manufacturing workflows, as well as best practices for their successful implementation.
Implementing the right production tools requires thoughtful planning and execution, ensuring that all team members understand their functionality and benefits. From automation software to ergonomic machinery, each tool plays a vital role in optimizing production lines and enhancing worker efficiency. This blog will delve into the most effective production tools, provide insights on their integration, and outline the best practices that will enable manufacturers to fully realize their potential. Embracing these strategies is essential for those striving to achieve operational excellence in a competitive marketplace.
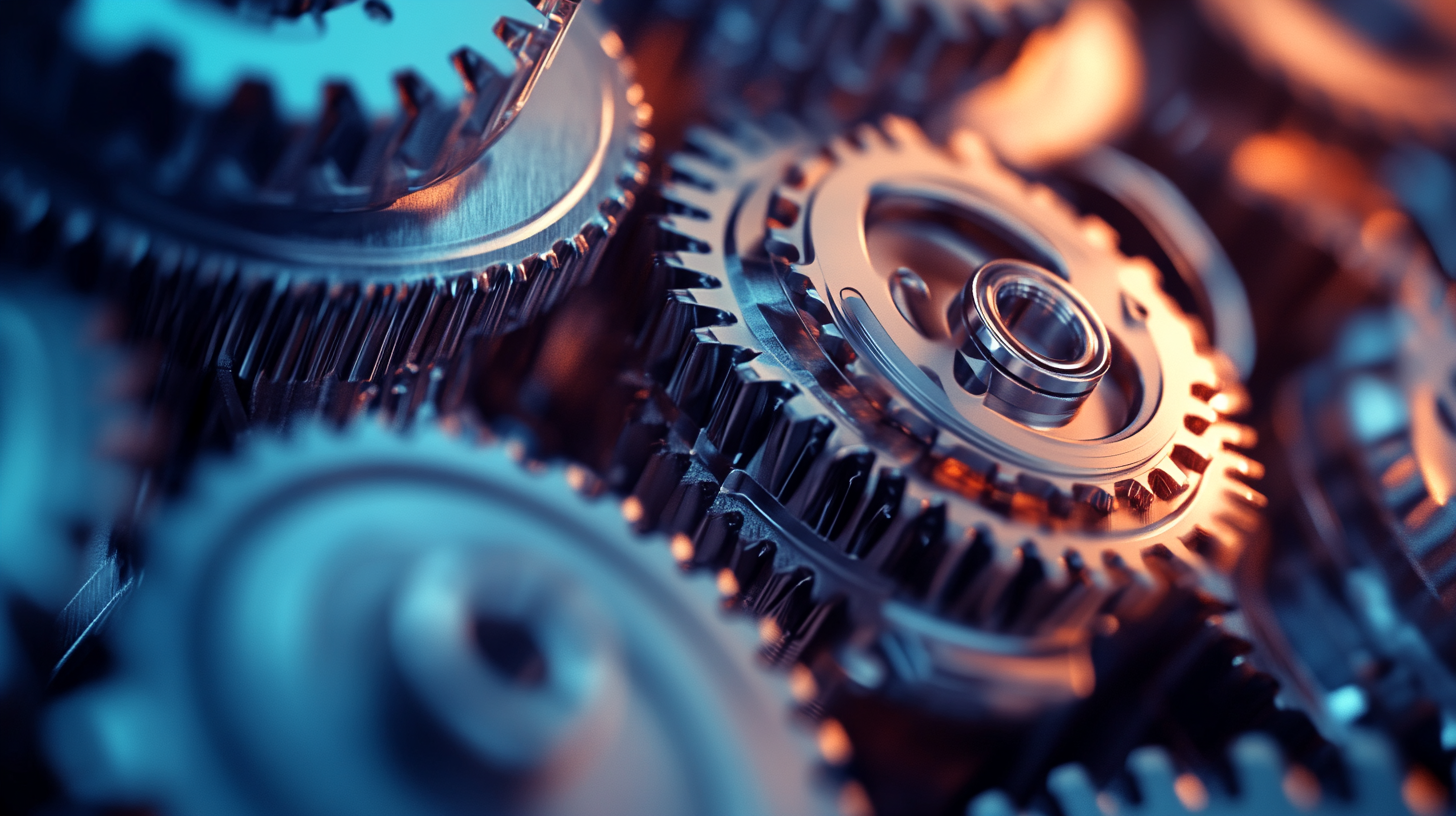
Key Production Tools Transforming Manufacturing Efficiency Today
In today’s rapidly evolving manufacturing landscape, leveraging key production tools has become essential for enhancing efficiency. With advancements in technology, several tools have emerged that transform traditional practices into streamlined processes. Automation software, for instance, allows manufacturers to reduce human error and improve consistency in production lines. By integrating automation, businesses can allocate resources more effectively, resulting in faster turnaround times and increased output. Another vital tool is data analytics, which provides insights into production performance. Manufacturers can monitor key metrics in real-time, identifying bottlenecks and inefficiencies within processes. This data-driven approach enables proactive decision-making, empowering teams to optimize operations continually. Implementing predictive analytics can further refine production schedules and inventory management, ensuring materials are available when needed, thus minimizing downtime. Sustainability tools also play a pivotal role in modern manufacturing by promoting eco-friendly practices. Companies are utilizing technology to track energy consumption and waste production, allowing for targeted improvements. By adopting sustainable practices, manufacturers not only enhance their operational efficiency but also meet the growing consumer demand for greener products. Ultimately, the strategic application of these production tools positions manufacturers at the forefront of an ever-competitive market.
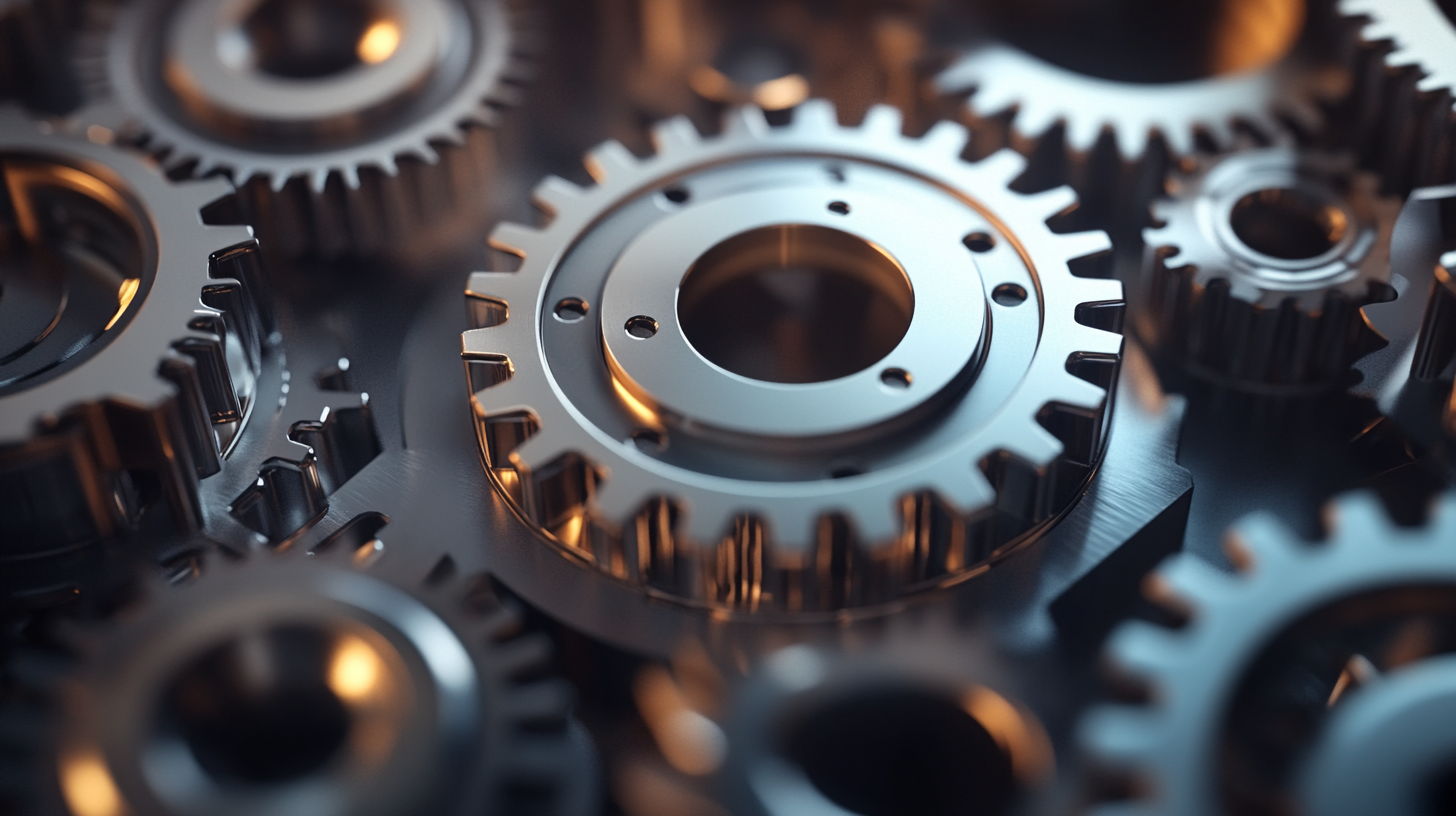
Analyzing Industry Data: Impact of Lean Manufacturing on Operational Performance
Lean manufacturing has emerged as a transformative approach in the manufacturing sector, focusing on streamlining operations and reducing waste. By analyzing industry data, we can see a clear correlation between the implementation of lean principles and improvements in operational performance. Companies that adopt lean practices often report enhanced productivity, lower operational costs, and quicker turnaround times.
One of the core tenets of lean manufacturing is the emphasis on continuous improvement, or "Kaizen." This practice encourages teams to constantly seek ways to enhance processes and eliminate inefficiencies. Data from various industries reveals that organizations embracing Kaizen not only experience substantial gains in efficiency but also foster a culture of innovation among employees. This shift not only drives immediate results but also promotes long-term sustainability and adaptability in the ever-evolving manufacturing landscape.
Furthermore, lean tools such as Value Stream Mapping and 5S (Sort, Set in order, Shine, Standardize, Sustain) provide manufacturers with clear frameworks for identifying bottlenecks and optimizing workflows. Industry benchmarks indicate that companies utilizing these tools typically achieve higher standards of quality and safety while minimizing resource consumption. As the manufacturing sector continues to face challenges posed by globalization and rapidly changing market demands, leveraging lean methodologies supported by robust data analysis becomes essential for maintaining competitive advantage.
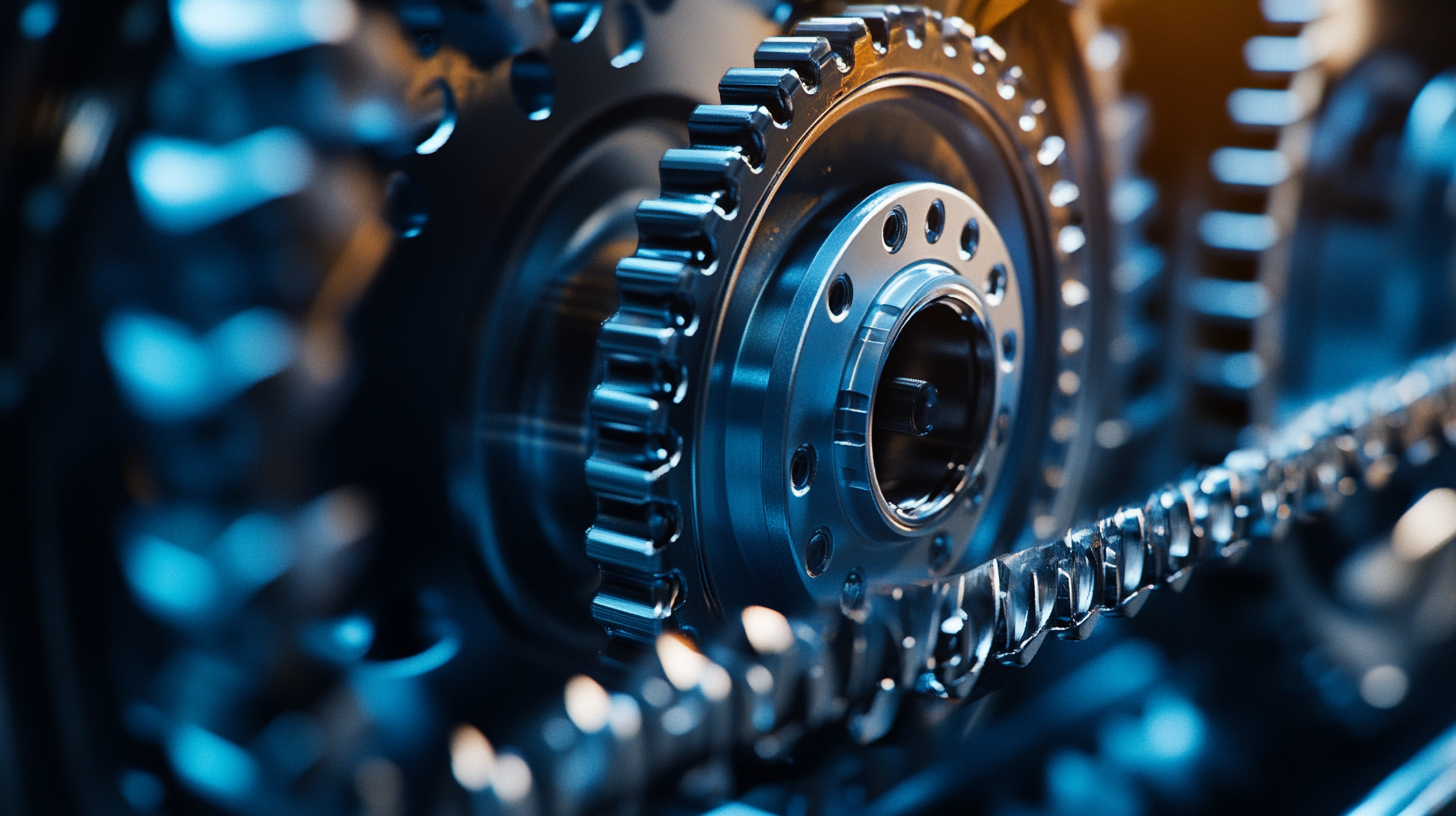
Integrating Technology: The Role of Automation in Streamlining Processes
In today's fast-paced manufacturing landscape, integrating technology through automation has become essential for streamlining processes and maximizing efficiency. Automation technologies, such as robotics and AI-driven software, enable manufacturers to accelerate production lines, reduce human error, and optimize resource allocation. By automating repetitive tasks, businesses can free up their workforce to focus on more strategic activities that require critical thinking and creativity.
The implementation of smart manufacturing systems, which leverage the Internet of Things (IoT), further enhances operational efficiency. These systems provide real-time data analytics, allowing manufacturers to monitor performance metrics and identify potential bottlenecks. With actionable insights at their fingertips, decision-makers can make informed adjustments to improve workflow and productivity. Moreover, predictive maintenance powered by machine learning can decrease downtime by anticipating equipment failures before they happen, ensuring a smooth and uninterrupted production process.
Integrating automation not only streamlines operations but also fosters a culture of continuous improvement. As companies adopt cutting-edge technologies, they can stay ahead of market demands and enhance their competitive edge. To successfully implement these automation tools, organizations must prioritize training and reskilling their workforce, ensuring that employees are equipped to work alongside advanced machinery and software. Embracing this synergy between human talent and technology is key to realizing the full potential of automation in the manufacturing sector.
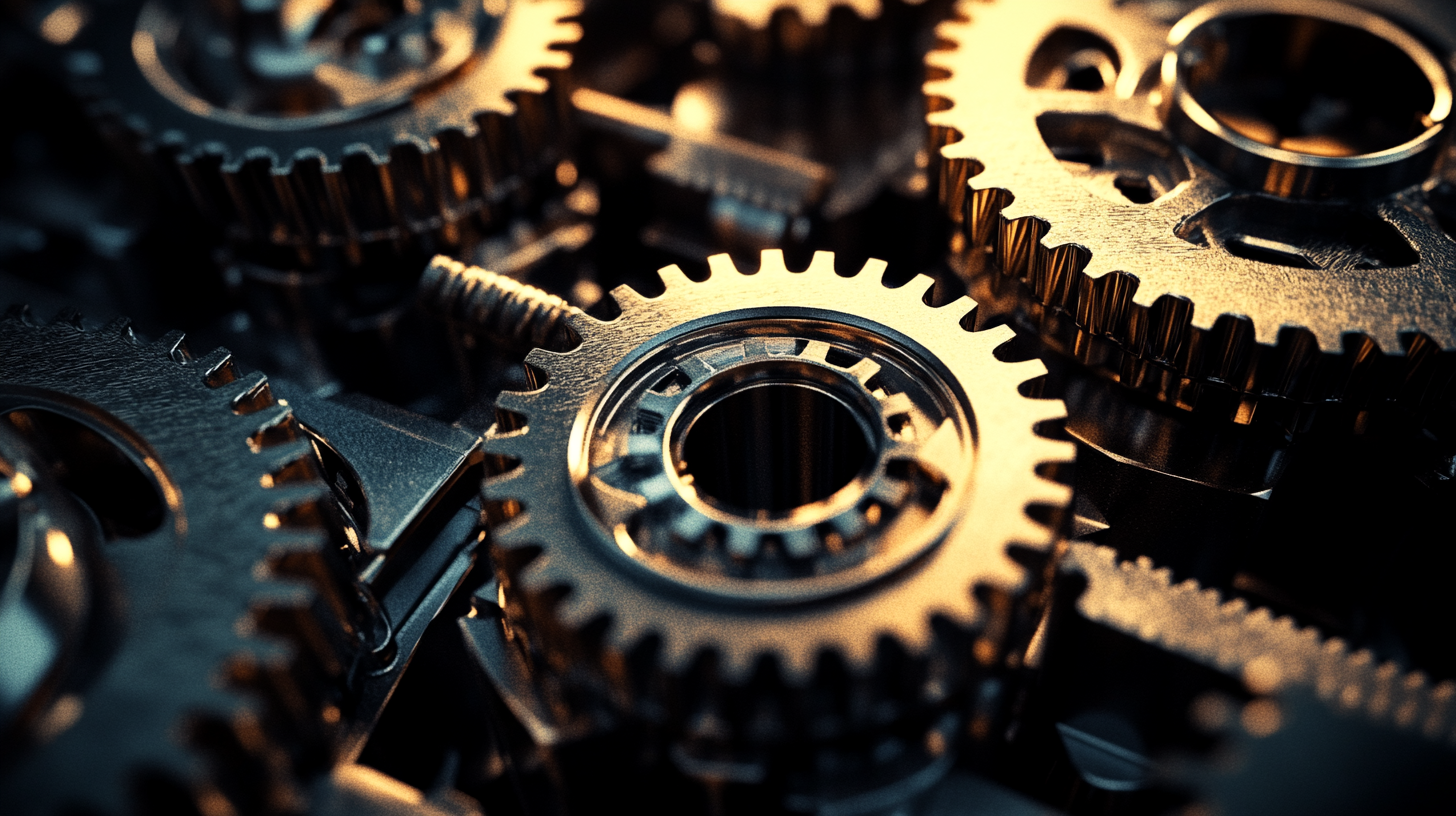
Best Practices for Implementing Production Tools: Strategies for Success
In the rapidly evolving landscape of manufacturing, implementing effective production tools is essential for enhancing efficiency and achieving strategic goals. Best practices for implementing these tools can significantly streamline operations, reduce costs, and improve overall productivity. According to a recent report from McKinsey & Company, companies that adopt advanced manufacturing technologies can see productivity gains of up to 30%, showcasing the importance of thoughtful tool integration.
One of the key strategies for successful implementation is leveraging data management throughout the entire lifecycle of production tools. As highlighted in emerging LLMOps practices, controlling data flow during pre-production, production, and post-production stages can lead to informed decision-making and resource optimization. For instance, effective sourcing and vendor management have been identified as crucial components in procurement management, where organizations aim to enhance their supply chains and minimize operational costs.
Moreover, fostering an adaptable workplace culture allows teams to embrace new technologies more readily. Companies that actively encourage training and development in production tool use report an increase in employee engagement and a decrease in resistance to change. This cultural adaptability, coupled with the integration of AI-driven solutions, can create a more responsive manufacturing environment poised to meet the challenges of 2024 and beyond. By employing these best practices, organizations can not only maximize operational efficiency but also position themselves as leaders in the competitive manufacturing sector.
Measuring ROI: Data-Driven Approaches to Evaluate Production Tool Effectiveness
Measuring ROI in manufacturing involves employing data-driven approaches to evaluate the effectiveness of production tools. According to a report by McKinsey, manufacturers that utilize advanced analytical tools can see productivity improvements of up to 20%. By effectively measuring the ROI of these tools, businesses can make informed decisions on investments and optimize their operations.
One critical method for assessment is the utilization of key performance indicators (KPIs) to quantify productivity gains. Metrics such as cycle time, defect rates, and labor efficiency are essential. A study by Deloitte revealed that companies that comprehensively track and analyze these KPIs can increase their profitability by up to 5% annually. This data-driven mindset helps organizations spotlight underperforming areas and prompts adjustments that enhance overall efficiency.
Moreover, integrating IoT-enabled devices can significantly bolster ROI measurement. According to a recent report from Statista, the IoT market in manufacturing is expected to reach $500 billion by 2023, enhancing data collection and real-time monitoring. This technology allows manufacturers to gain precise insights into their operations, enabling continuous improvement aligned with data-backed strategies. By understanding the tangible benefits derived from these tools, organizations can justify their investments and pave the way for sustainable growth.