Revolutionizing Precision Manufacturing with Bespoke Carbide Tool Solutions
In recent years, the landscape of precision manufacturing has undergone significant transformation, driven by advancements in technology and an increased demand for customized solutions. According to a report by MarketsandMarkets, the global custom tooling market is projected to reach USD 2.63 billion by 2025, with a compound annual growth rate (CAGR) of 6.5%. This growth is fueled by the need for tailored manufacturing processes that enhance productivity, efficiency, and product quality. As industries ranging from aerospace to automotive seek to optimize their operations, the relevance of **Custom Carbide Tooling** has never been more pronounced.
Custom carbide tooling offers manufacturers the unique ability to create tools specifically designed for their production requirements, allowing for greater precision and reduced waste. A study published by TWI Global highlights that custom tool solutions can lead to performance improvements of up to 30% compared to off-the-shelf alternatives. As businesses strive to innovate and stay competitive, the integration of bespoke carbide tooling solutions is becoming a key differentiator in achieving operational excellence and meeting the exacting standards of today’s market.
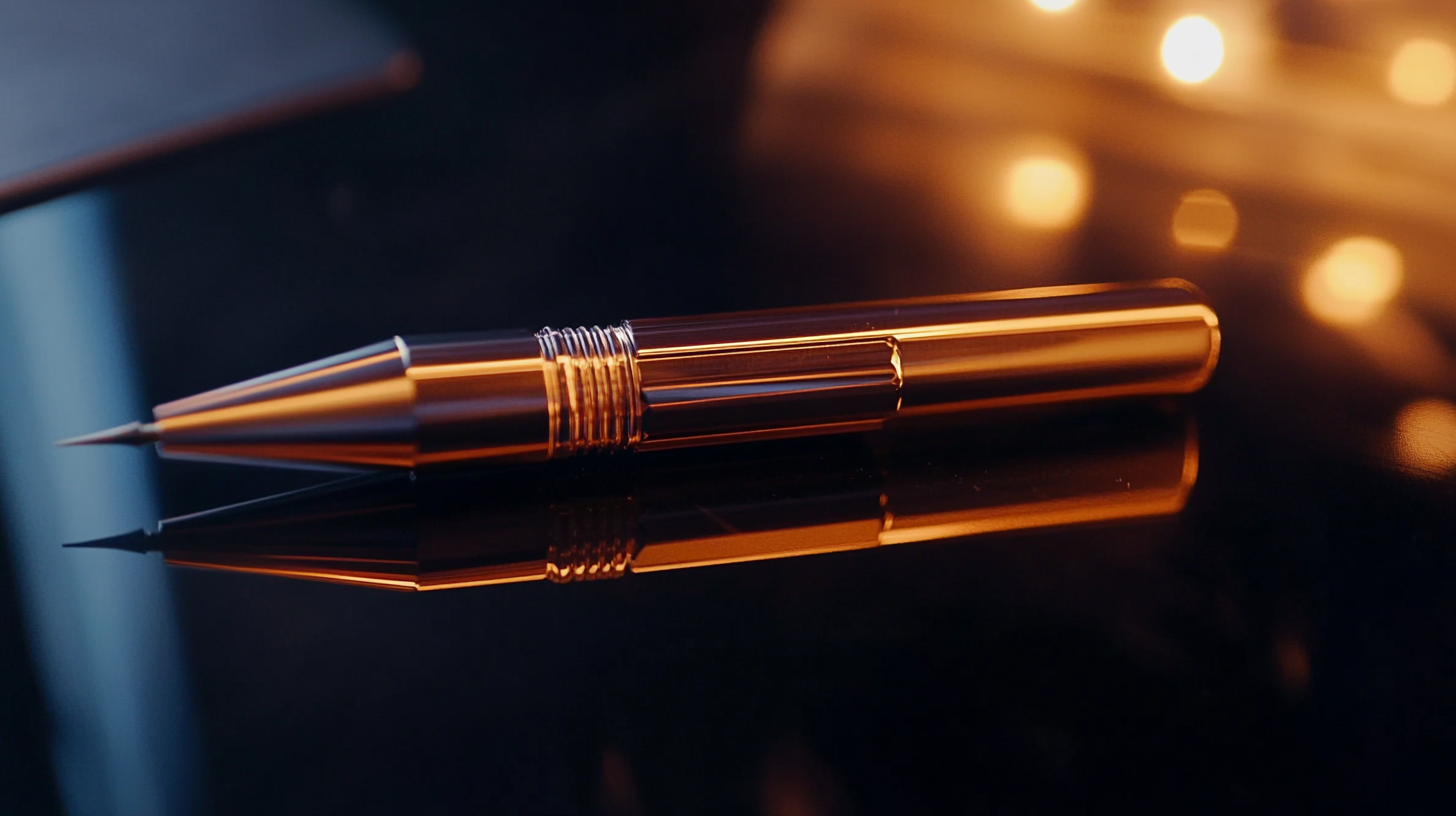
The Evolution of Carbide Tools in Precision Manufacturing
The evolution of carbide tools has profoundly transformed the landscape of precision manufacturing. Initially introduced in the mid-20th century, carbide tools were celebrated for their hardness and durability, revolutionizing machining processes. Over the decades, advancements in material science have led to the development of high-performance carbide alloys, enhancing cutting efficiency and tool life. These innovations paved the way for achieving tolerances that were previously thought impossible, allowing manufacturers to meet the stringent demands of modern industries. As industries evolved, so did the requirements for tools. The bespoke nature of today’s manufacturing landscape calls for tailored solutions that accommodate specific production challenges. Carbide tools have responded to this demand by offering customizable shapes, sizes, and coatings to suit various applications. With advances in computer-aided design (CAD) and manufacturing (CAM), manufacturers can now create tools that are specifically engineered for unique jobs, leading to improved performance and reduced waste. Moreover, the transition towards automation and smart manufacturing systems necessitates tools that can reliably integrate with advanced technologies. Innovations in carbide tool design, incorporating features such as self-sharpening edges and enhanced chip management, are facilitating this integration. As industries continue to embrace digital transformation, the capability of bespoke carbide tool solutions will be crucial for sustaining competitiveness and ensuring precision in the manufacturing process.
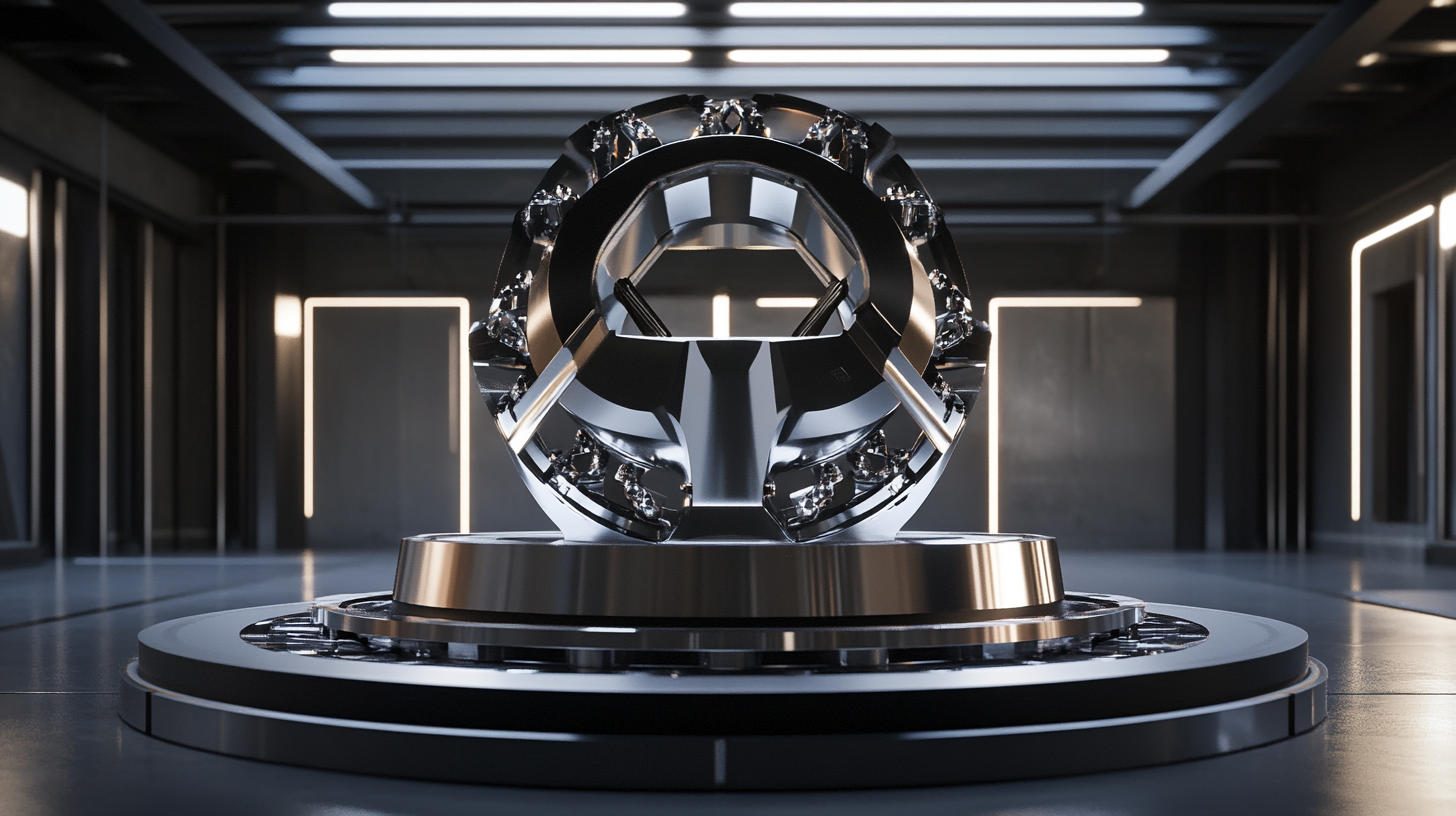
Tailoring Carbide Solutions: Meeting Specific Production Needs
The Precision Manufacturing industry is undergoing a transformative shift, particularly in the realm of bespoke carbide tool solutions that are designed to meet specific production needs. The 2024 Shanghai International Automotive Exhibition highlights this trend, showcasing innovations that target the automotive sector and beyond. With the global metal cutting tools market expected to exceed $44.4 billion in 2023, the demand for tailored solutions is greater than ever, driven by advancements in industries such as aerospace, construction, and machinery.
In response to this growing demand, companies are investing in custom carbide solutions that cater to unique manufacturing processes. By employing a combination of advanced materials and cutting-edge technology, manufacturers can enhance tool performance, reduce production costs, and improve overall efficiency. Reports suggest that the compound annual growth rate for the metal cutting tool market will surpass 5% from 2024 to 2032. This surge indicates that businesses are increasingly prioritizing precision and customization in their production strategies.
Moreover, the integration of industrial internet technologies is becoming paramount for facilitating these bespoke solutions. As the Chinese government emphasizes industrial internet development, manufacturers are finding ways to leverage data analytics and connected systems to optimize their tool solutions further. This evolution not only supports individual production needs but also aligns with the broader trends of sustainability and efficiency enhancements across the manufacturing landscape.
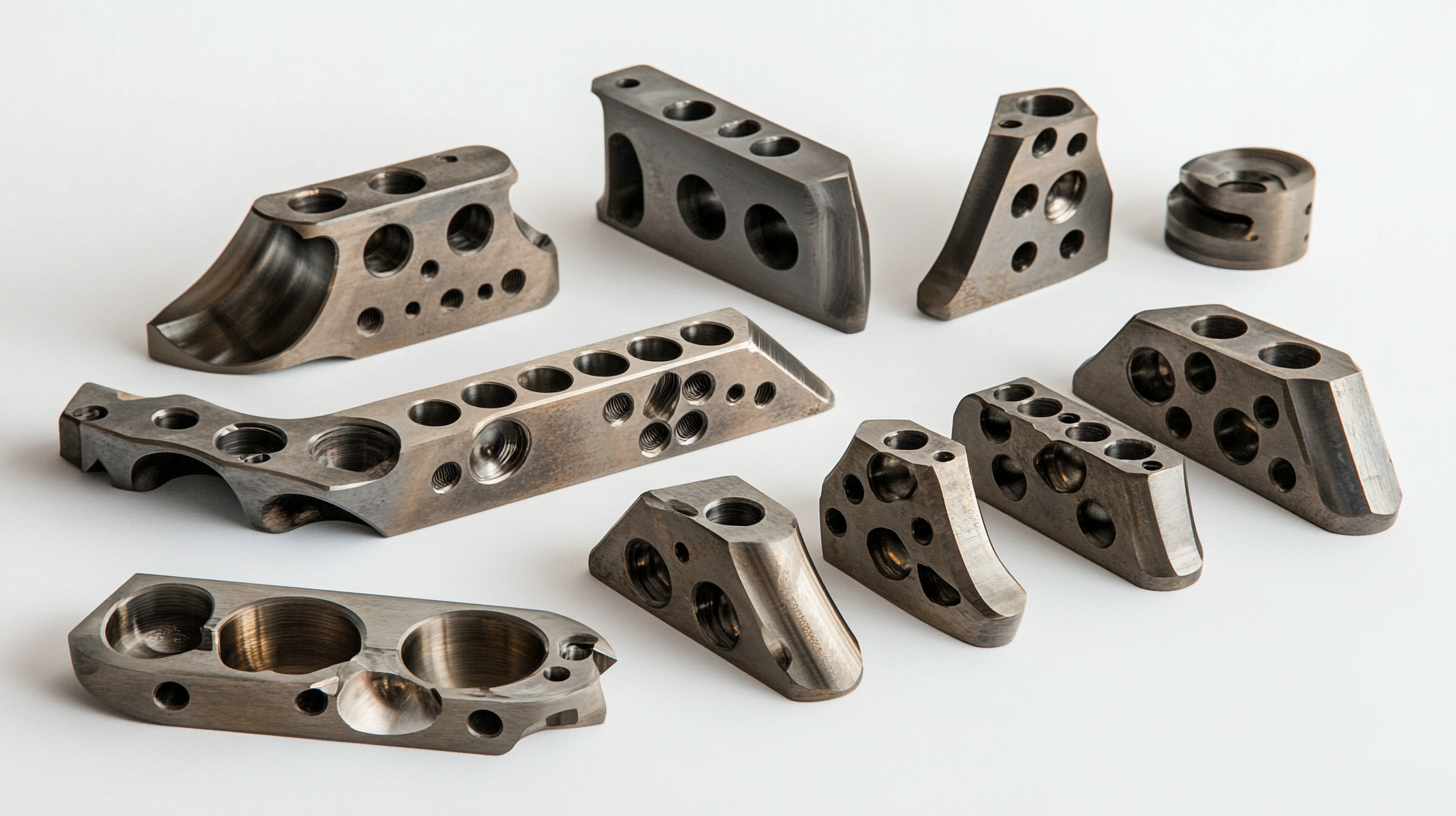
The Impact of Customized Tools on Efficiency and Quality
In the realm of precision manufacturing, customized tools have emerged as a game-changer in enhancing efficiency and quality. According to a report by the International Journal of Advanced Manufacturing Technology, companies that implement bespoke tooling solutions experience up to a 25% increase in productivity. This is largely attributed to the fact that customized carbide tools are specifically designed to meet the unique requirements of particular machining processes, minimizing waste and maximizing output.
The influence of tailored tools extends beyond productivity; it significantly impacts the quality of the finished product. According to a study by the Association for Manufacturing Technology, manufacturers using bespoke tools report a reduction in defects by as much as 30%. This improvement is due to the precise engineering of customized tools, which align perfectly with the specifications of the materials being used. As manufacturers face increasing pressure to deliver high-quality products, the demand for customized carbide tools continues to rise, reinforcing their value in the industry.
Furthermore, as the Industry 4.0 trend continues to gain traction, the integration of data-driven decision-making processes has become essential. Companies utilizing advanced metrics in conjunction with bespoke tooling can optimize their manufacturing processes, leading to a reduction in setup times and increased machine life. According to Metrics & Models in Manufacturing, those who adopt this integrated approach can see up to a 20% reduction in operational costs, showcasing the tangible benefits of investing in tailor-made solutions for precision manufacturing.
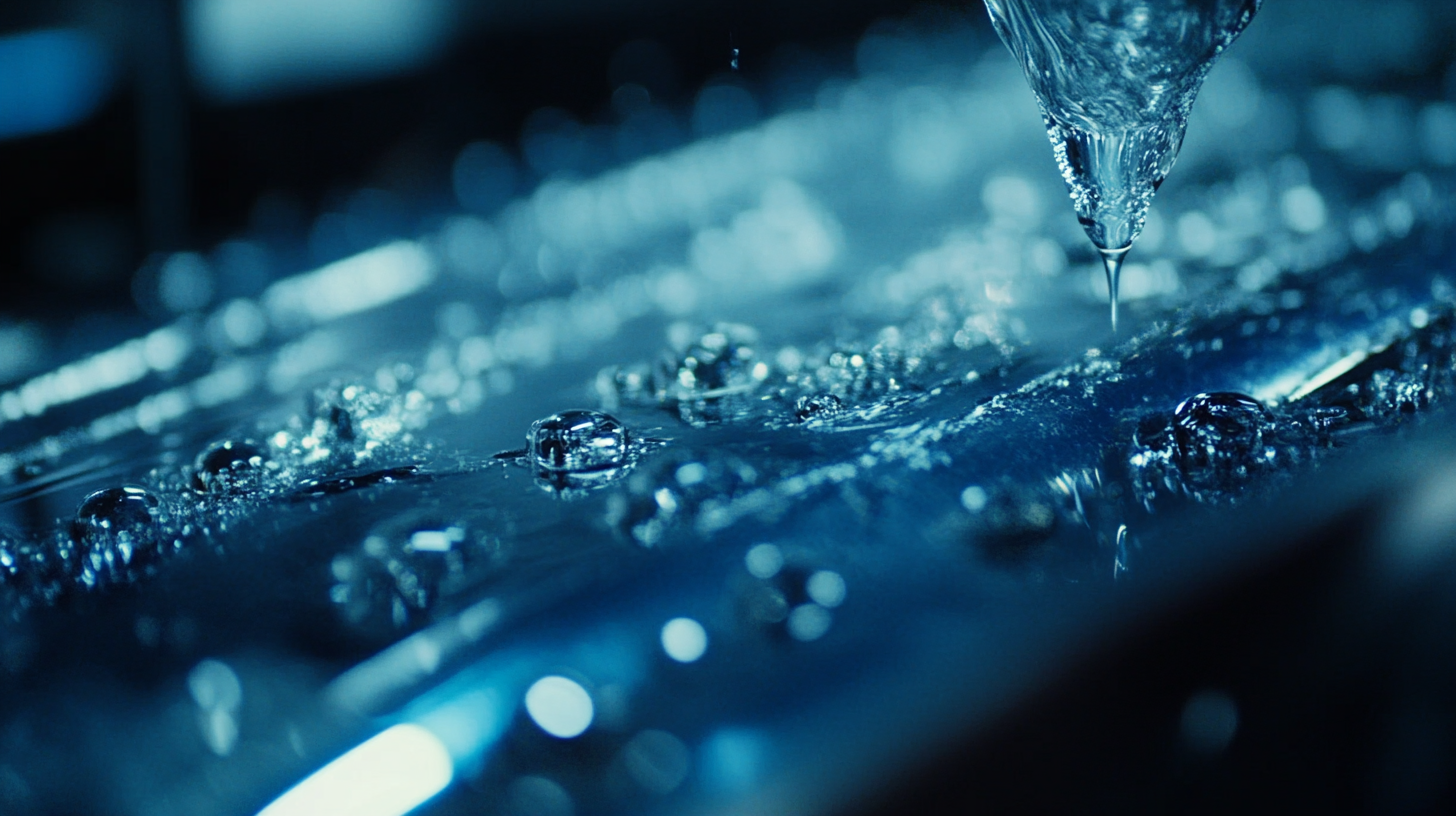
Innovative Technologies Driving Bespoke Carbide Manufacturing
The realm of bespoke carbide manufacturing is undergoing a significant transformation, driven by innovative technologies that cater to the precise demands of modern industries. Notably, research from SmarTech Publishing in October 2022 reveals a staggering forecast indicating that the automotive sector is poised to generate $9 billion in revenue solely from 3D-printed end-use parts, marking an eightfold increase since 2019. This rapid growth signifies a paradigm shift in precision manufacturing, where customization and efficiency are paramount.
In parallel, the global market for carbide abrasives is projected to rise from $425 million in 2022 to $670.6 million by 2029, with a compound annual growth rate (CAGR) of 6.6%. This expansion underscores the escalating demand for tailored tooling solutions that enhance operational efficiency. Furthermore, the innovation in SIC production and abrasive brush technology is refining the manufacturing processes, leading to improved performance and durability of carbide tools.
The index of turning tool markets also reflects a promising trajectory, predicted to surpass $4.63 billion in 2023. With the advent of Industry 4.0 and intelligent manufacturing frameworks, the CAGR for this sector from 2024 to 2032 is expected to be 6.3%. These advancements showcase how bespoke carbide tool solutions are not just responding to industry needs but are also setting the stage for a new era of precision and customization in manufacturing practices.
Case Studies: Success Stories in Precision Tool Solutions
In the realm of precision manufacturing, custom carbide tool solutions have emerged as a game-changer, dramatically enhancing efficiency and accuracy. Industry reports indicate that tailored tools can increase productivity by up to 20%, making them a strategic choice for manufacturers striving for competitive advantage. One fascinating case study examined a leading aerospace component manufacturer that adopted bespoke carbide tools. By customizing tool geometries to fit specific applications, the company reported a 30% reduction in machining time and an impressive increase in part tolerances, minimizing waste and rework.
Another notable success story comes from the automotive sector, where one manufacturer switched to customized carbide tooling for its engine production line. This transition not only optimized their cutting processes but also yielded a significant improvement in tool lifespan—up to 40%. According to the latest reports from the Precision Tooling Association, manufacturers investing in bespoke solutions are likely to experience a return on investment within just six months, largely due to decreased cycle times and improved operational efficiencies.
These examples highlight how precision tool solutions are reshaping the landscape of manufacturing. As companies increasingly leverage data-driven strategies to tailor their tooling, the role of bespoke carbide solutions in fostering innovation and streamlining production cannot be overstated. With each success story, the industry collectively moves toward a future where precision and customization are paramount.