Maximize Performance and Reduce Maintenance Costs with 7 Essential Tips for Indexable Milling
In the ever-evolving world of manufacturing, the efficiency of machining processes significantly impacts both productivity and cost management. Indexable milling has emerged as a crucial technique, with studies indicating that it can reduce tool replacement costs by up to 30% compared to traditional methods. According to a report from Grand View Research, the global indexable tools market is projected to reach a value of USD 15.9 billion by 2025, driven by increasing demand for precise machining and the need for sustainable operations in various industrial sectors.
To remain competitive, manufacturers must focus on optimizing their milling processes not only to achieve superior performance but also to lower maintenance expenses. Implementing effective strategies in indexable milling can lead to heightened productivity, enhanced tool life, and minimized downtime. In this blog post, we will explore seven essential tips that can help you maximize the performance of your indexable milling operations while simultaneously reducing maintenance costs. By adopting these best practices, businesses can leverage the full potential of their machining capabilities and achieve remarkable economic benefits.
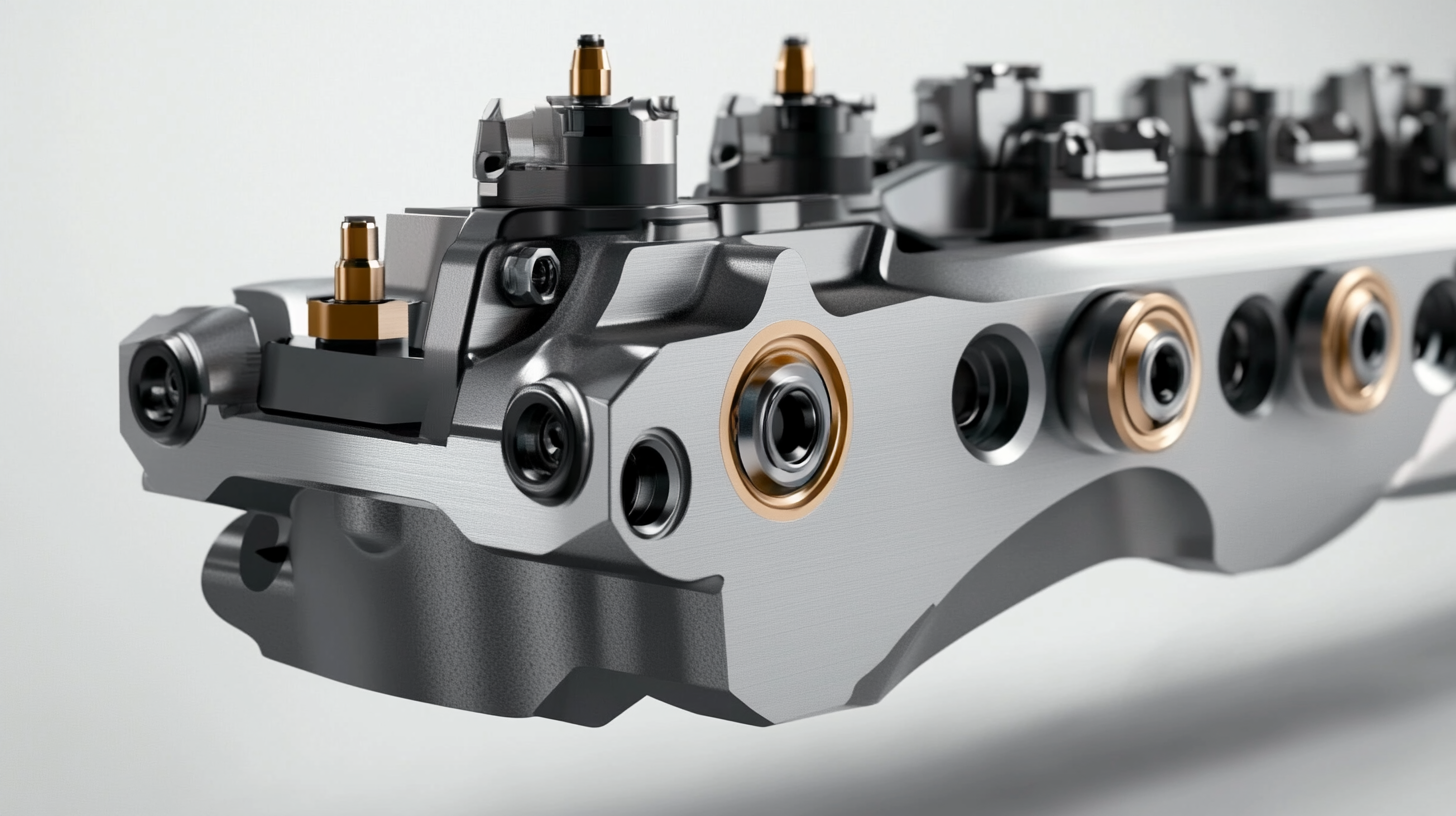
Understanding the Importance of Indexable Milling in Modern Manufacturing
Indexable milling has emerged as a crucial component in modern manufacturing, playing a significant role in optimizing production processes. The importance of this method lies in its ability to facilitate fast and effective material removal while ensuring high precision. As industries face ever-changing economic conditions, understanding the benefits of indexable milling can empower companies to enhance their operational efficiency and reduce maintenance costs. With sharp cutting tools designed for shear deformation, manufacturers can achieve superior results in their machining processes. As the U.S. strives to retain its competitive edge in the global manufacturing landscape, embracing innovative strategies is vital. Indexable milling technology offers a pathway for not only preserving the quality of manufactured goods but also fostering innovation in manufacturing processes. With manufacturers focusing on refining their machining capabilities, there is an opportunity to increase productivity and streamline operations, which becomes essential in an era of technological advancement. Moreover, as construction companies seek to navigate economic fluctuations, integrating effective manufacturing strategies that include indexable milling can ultimately lead to sustainable growth. By prioritizing such advanced techniques, businesses can capitalize on efficiency gains while simultaneously reducing the frequency and costs associated with maintenance, setting the stage for long-term success in an increasingly competitive environment.
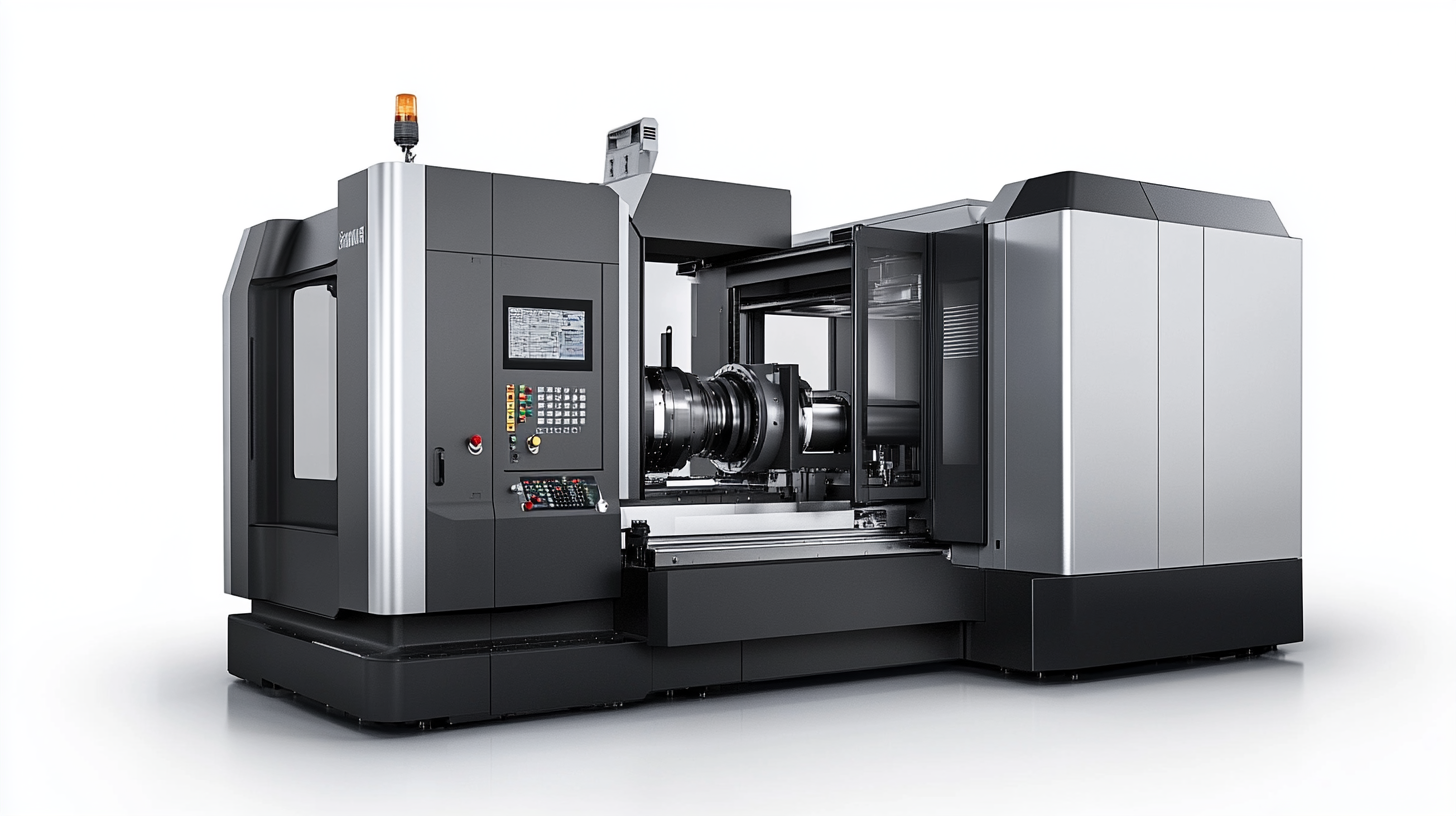
Key Factors Influencing Cutting Tool Performance and Longevity
When it comes to indexable milling, understanding the key factors that influence cutting tool performance and longevity is essential for optimizing manufacturing processes. A study by the Metal Cutting Institute highlights that up to 30% of production costs can be attributed to tooling failures. Therefore, implementing strategies that enhance the cutting tool's lifespan not only leads to better performance but also significantly reduces maintenance costs.
One of the primary factors affecting the performance of cutting tools is the material composition. Carbide inserts, for instance, are known for their hardness and wear resistance; they can deliver up to three times the life compared to high-speed steel tools, according to a report from Global Tooling Solutions. Moreover, the use of advanced coatings, such as TiAlN or AlTiN, can further increase tool life by providing a protective layer that reduces friction and heat buildup during cutting operations.
Furthermore, the cutting parameters, including speed, feed rate, and depth of cut, play a crucial role in maximizing tool efficacy. The Engineering Tool Box suggests that optimizing these parameters can enhance the cutting tool's performance by reducing tool wear rates by nearly 40%. Additionally, maintaining proper coolant application not only aids in chip removal but also helps in maintaining the tool temperature, avoiding premature tool failure. By focusing on these key factors, manufacturers can achieve significant improvements in both performance and cost efficiency in their milling operations.
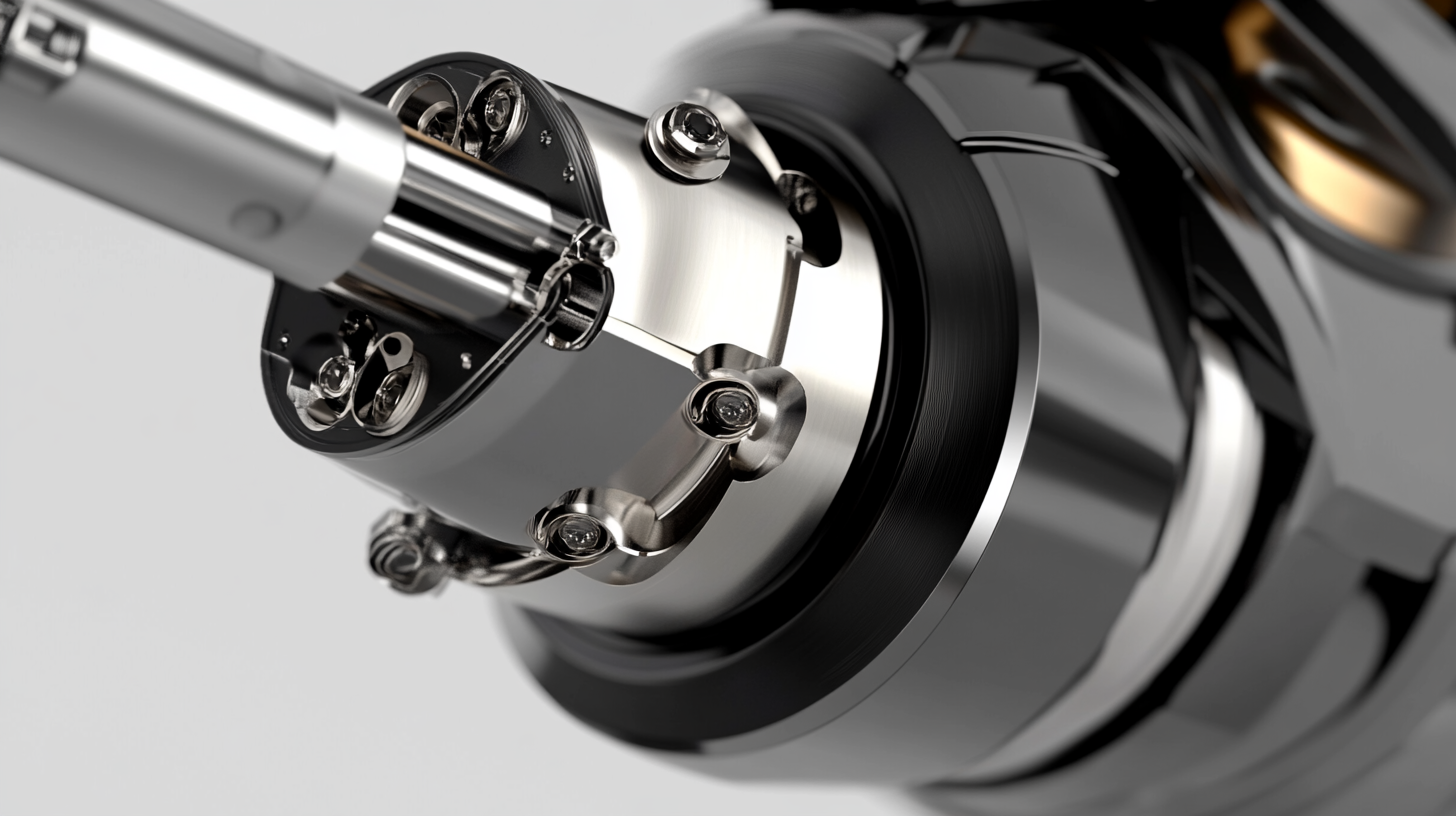
Strategies to Optimize Cutting Parameters for Enhanced Efficiency
In the realm of manufacturing, the optimization of cutting parameters is crucial for enhancing efficiency and maximizing productivity in indexable milling operations. Recent data from the Manufacturing Technology Association indicates that fine-tuning these parameters can lead to a reduction in cycle times by as much as 30%, allowing companies to increase their output without additional capital expenditures.
One of the key strategies for optimizing cutting parameters is selecting the right cutting speed and feed rate. According to a report by the Metalworking Industry Association, proper alignment of these parameters allows manufacturers to attain optimal chip formation, reducing tool wear and increasing tool life by 20-50%. This not only enhances the performance of the milling operation but also drastically minimizes maintenance costs associated with premature tool replacements.
Additionally, implementing advanced monitoring techniques, such as utilizing IoT sensors for real-time data analysis, can provide manufacturers with insights into tool performance and wear rates. An industry study highlighted that companies that adopted predictive maintenance strategies saw a reduction in maintenance costs by up to 40%. By leveraging such technologies, organizations can ensure that their milling operations remain efficient and cost-effective, ultimately driving profitability and competitiveness in an ever-evolving market.
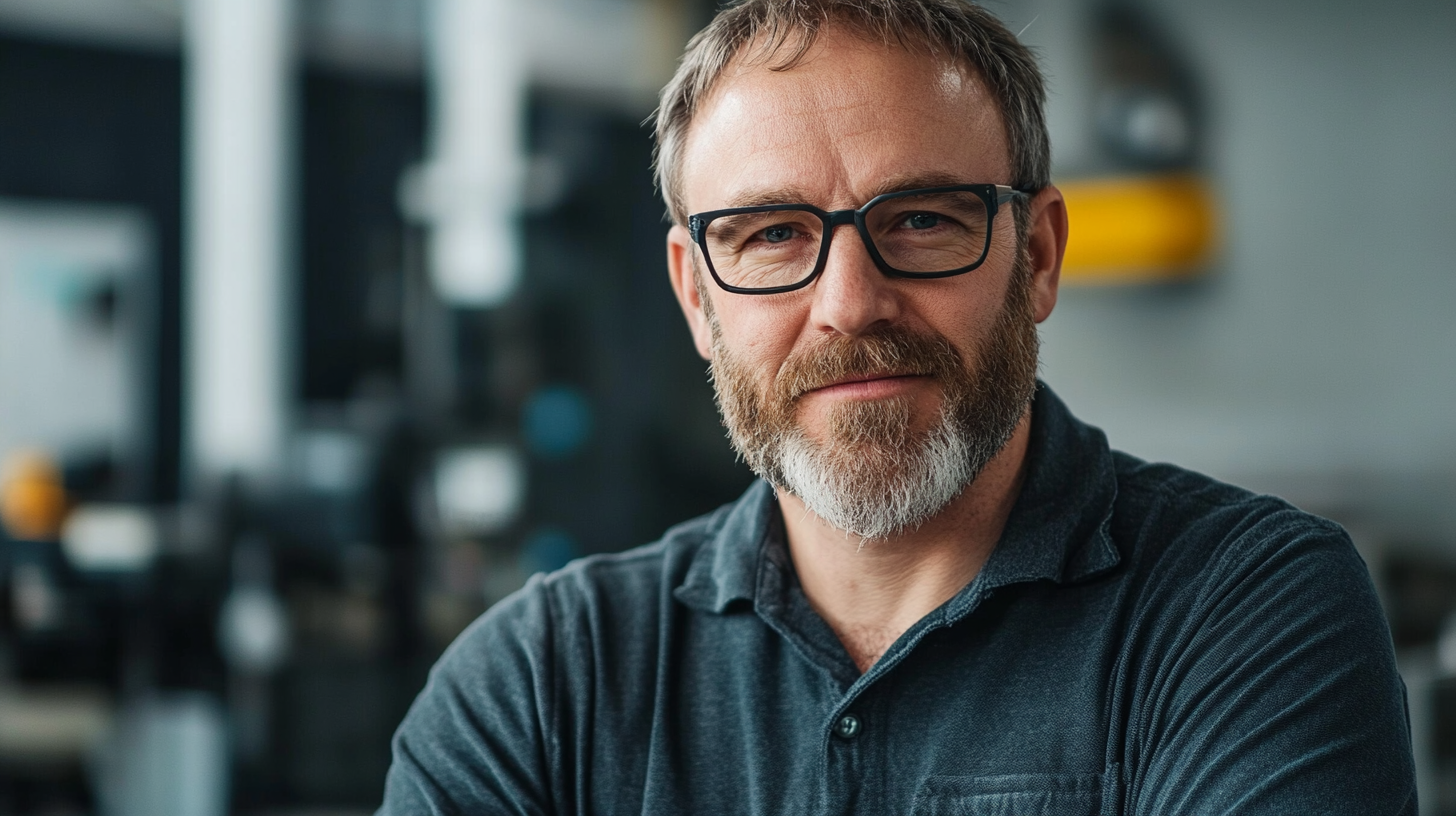
Cost-Benefit Analysis: Balancing Performance and Maintenance Expenses
In the competitive landscape of manufacturing, the balance between performance and maintenance expenses is crucial for optimizing productivity. A recent report from the Manufacturing Technology Association (MTA) indicates that ineffective maintenance strategies can inflate operational costs by up to 30%. This underscores the necessity for manufacturers to adopt a strategic approach to their tooling—particularly in indexable milling, where both performance enhancements and maintenance costs can heavily influence the bottom line.
Investing in high-quality indexable cutting tools can significantly reduce maintenance fees. According to a study by the National Tooling and Machining Association (NTMA), tools that last longer can decrease the frequency of replacements, thereby lowering costs associated with tool procurement and downtime. Specifically, tools that provide a longer cycle life can enable manufacturers to save around 25% on total operational costs. This highlights the importance of selecting the right tool geometry and material for specific applications to maximize efficiency and reduce wear.
Furthermore, an effective cost-benefit analysis reveals that while the initial investment in high-performance tools might be higher, the long-term savings derived from reduced maintenance and improved productivity offer a compelling return on investment. In fact, the Advanced Manufacturing Office notes that companies utilizing data-driven maintenance strategies achieve a reduction of up to 70% in maintenance-related expenses. By regularly analyzing performance metrics and adjusting maintenance schedules, manufacturers can strategically align their operational capabilities with financial goals, ensuring sustained profitability in a dynamic market.
Best Practices for Tool Selection and Management in Indexable Milling
When it comes to indexable milling, effective tool selection and management are crucial in maximizing performance while minimizing maintenance costs. One of the best practices in this area is to prioritize tool quality. High-quality indexable tools often feature advanced materials and coatings that enhance their durability and cutting performance. Investing in premium tools can significantly reduce the frequency of replacements and improve your machining processes, leading to longer tool life and better surface finishes.
Another important aspect of tool management is maintaining a well-organized inventory. Keeping track of tool types, specifications, and usage patterns allows for more effective planning and reduces downtime. Utilizing advanced inventory management systems or software can help operators make informed decisions regarding tool selection based on current projects and machining requirements. Furthermore, establishing a regular maintenance routine for tools, including cleaning and sharpening, can facilitate optimal performance and prevent costly failures.
Finally, considering the compatibility of tools with machine capabilities is essential. Before selecting a tool, understanding the specific requirements of your milling operations, such as cutting speed, feed rate, and material being machined, ensures that the tools you choose will perform effectively. Collaborative discussions with tool manufacturers can also provide insights into the best options tailored to your needs, helping you streamline operations and maximize productivity in indexable milling.